Second Set of Images
My pieces are identified by a three letter/digit code stamped in the footring. ‘CVR’, ‘CEL’ and so forth, are the codes.
Featured piece with favourite glaze
CVR combines my favourite glaze (detailed in the text below) with one of my iron silicate aventurine glazes.
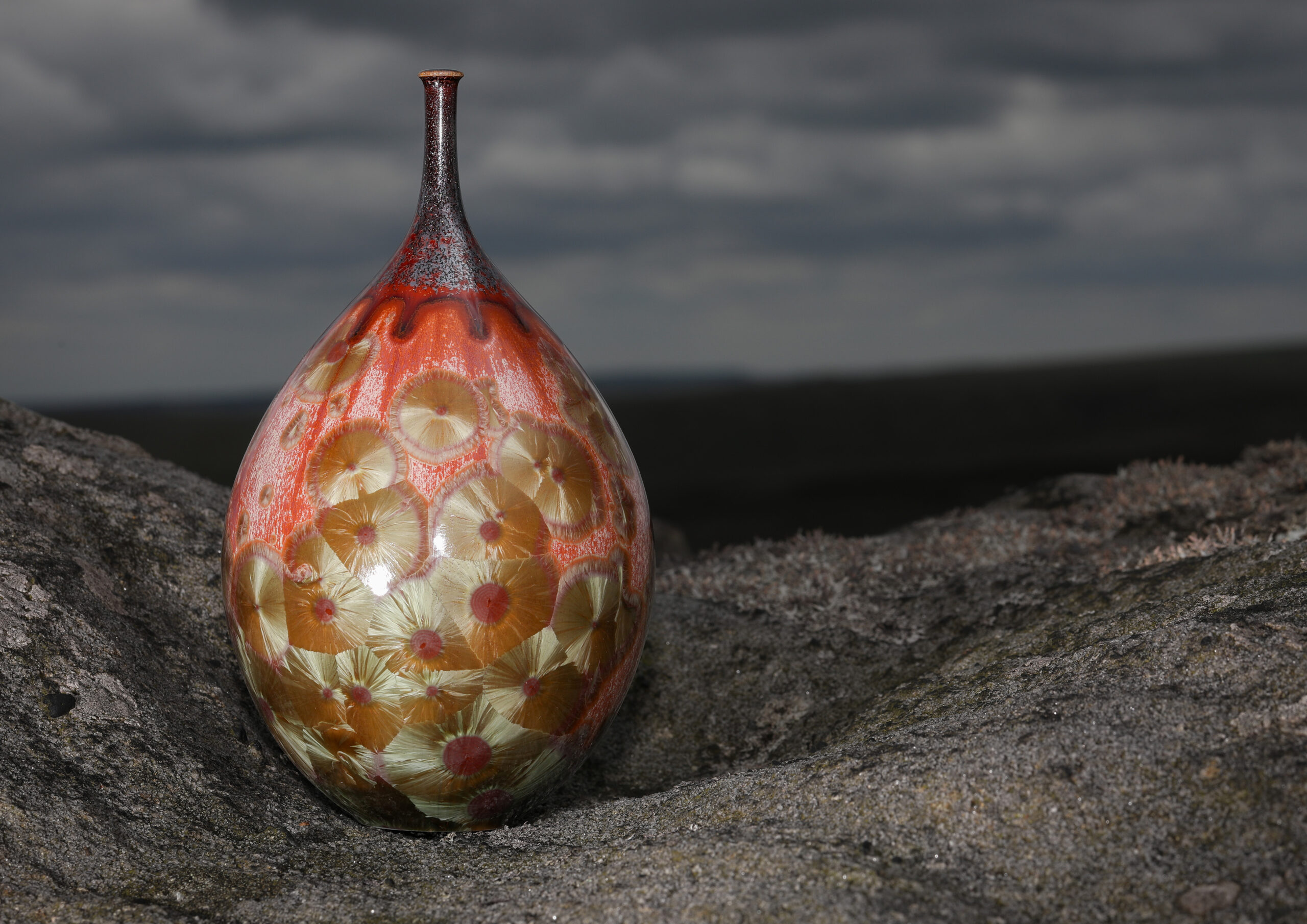
CVR pictured on an outcrop of gritstone in the uplands of Northern England. 2024.
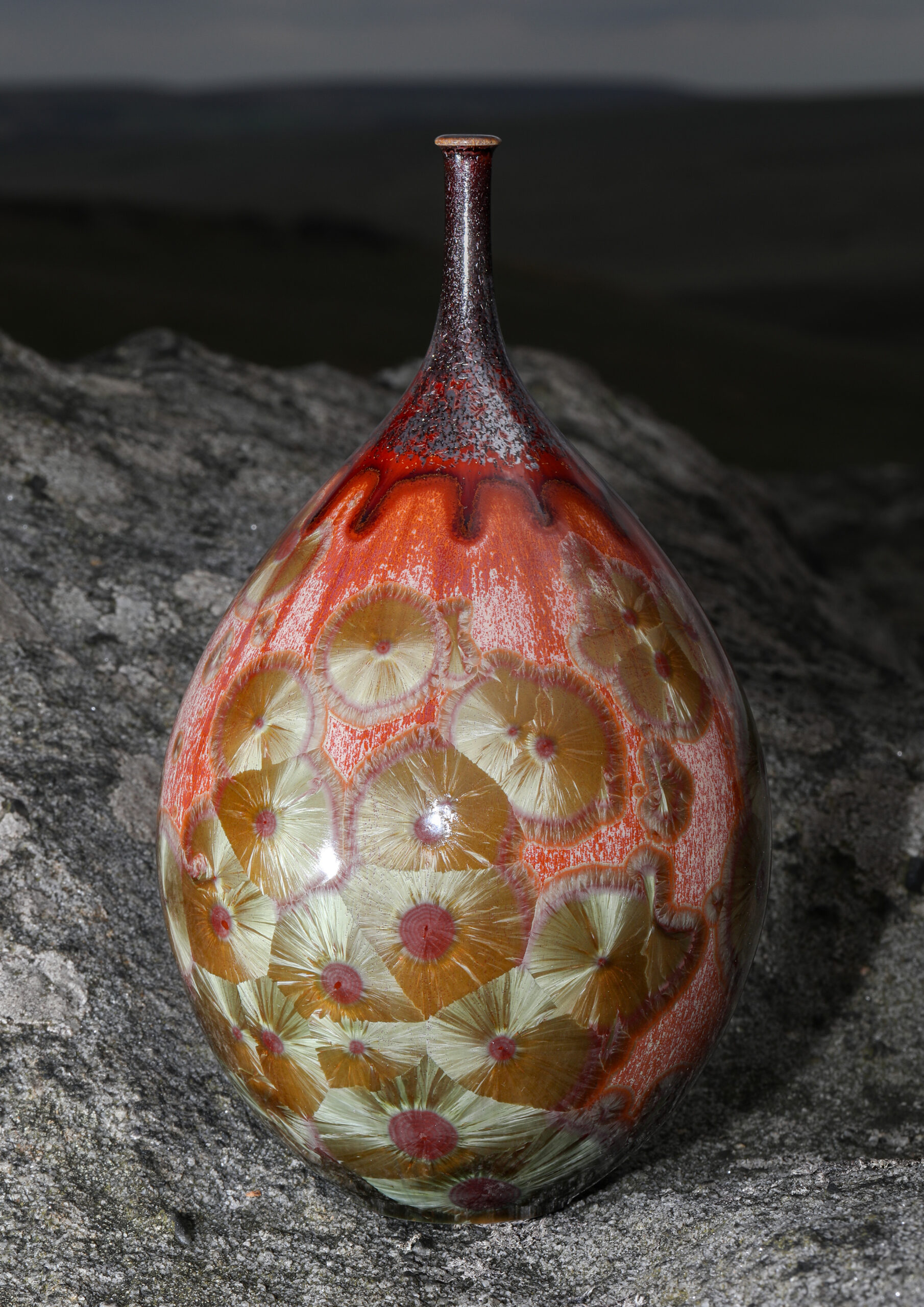
CVR pictured on an outcrop of gritstone in the uplands of Northern England.
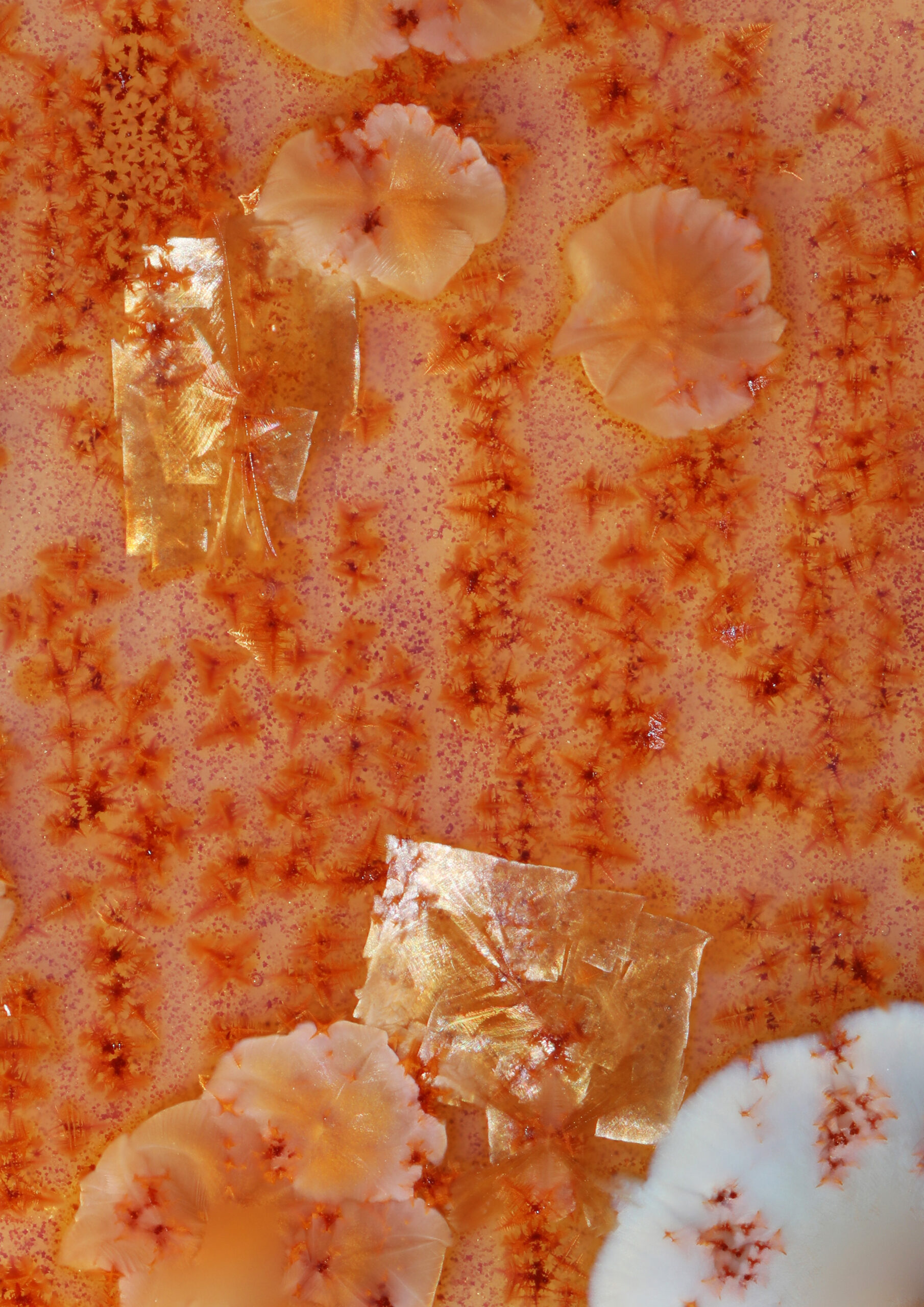
Magnified view of the secondary crystals of the CVR glaze. The region shown here is 2.7mm x 3.8mm in size.
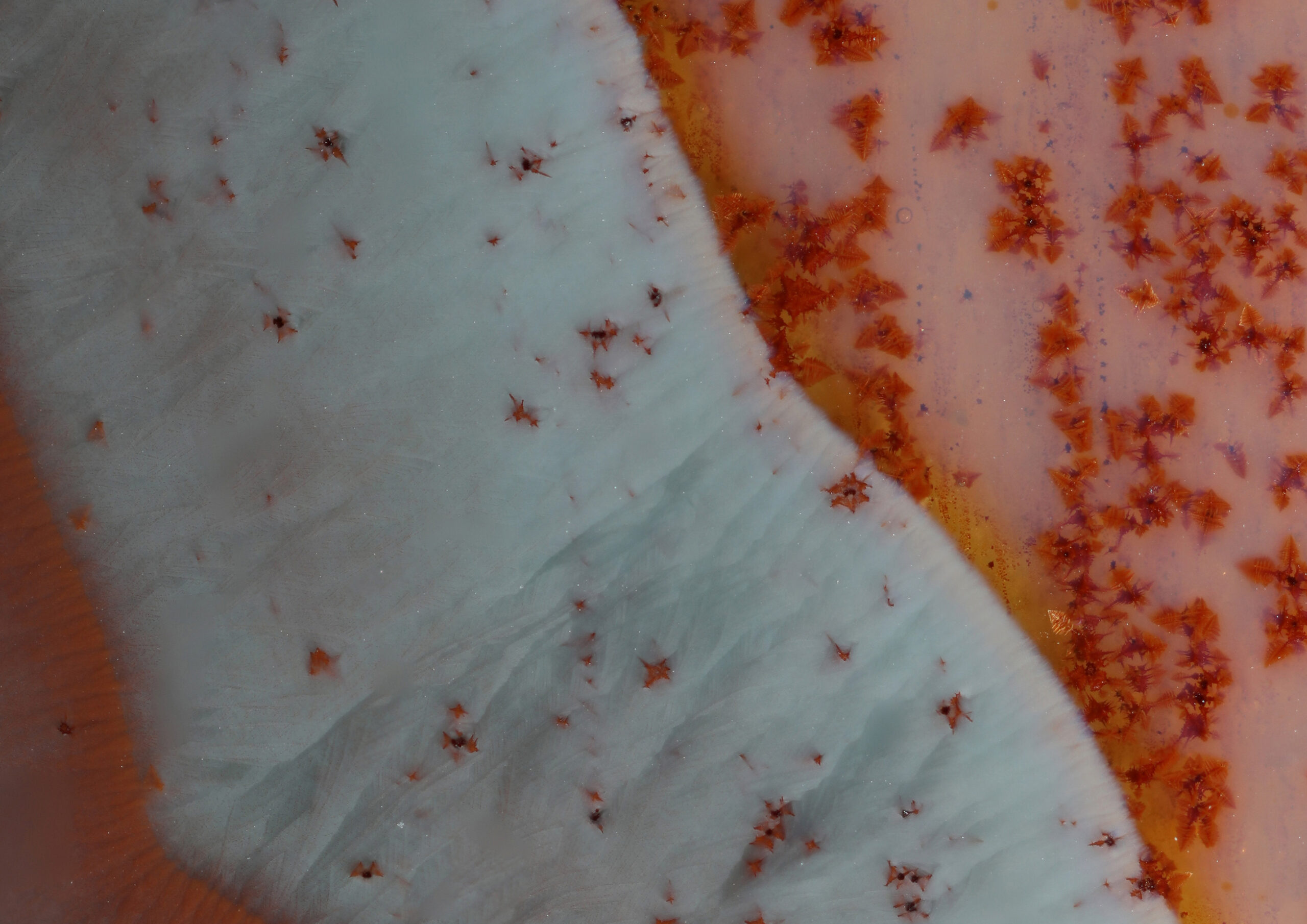
Magnified view of the secondary crystals in the CVR glaze. The region shown here is 3.2mm x 2.3mm in size.
Additional Images
I have selected these four images of my favorite pieces each taken in a different location in the north of England. CGC and CWJ are both glazed with a variant of my favourite glaze, the same as CVR. CEL and CRK have different chemistires that share the property of producing a powerful development of secondary crystals.

CEL pictured against a backdrop of bluebells. 2022.
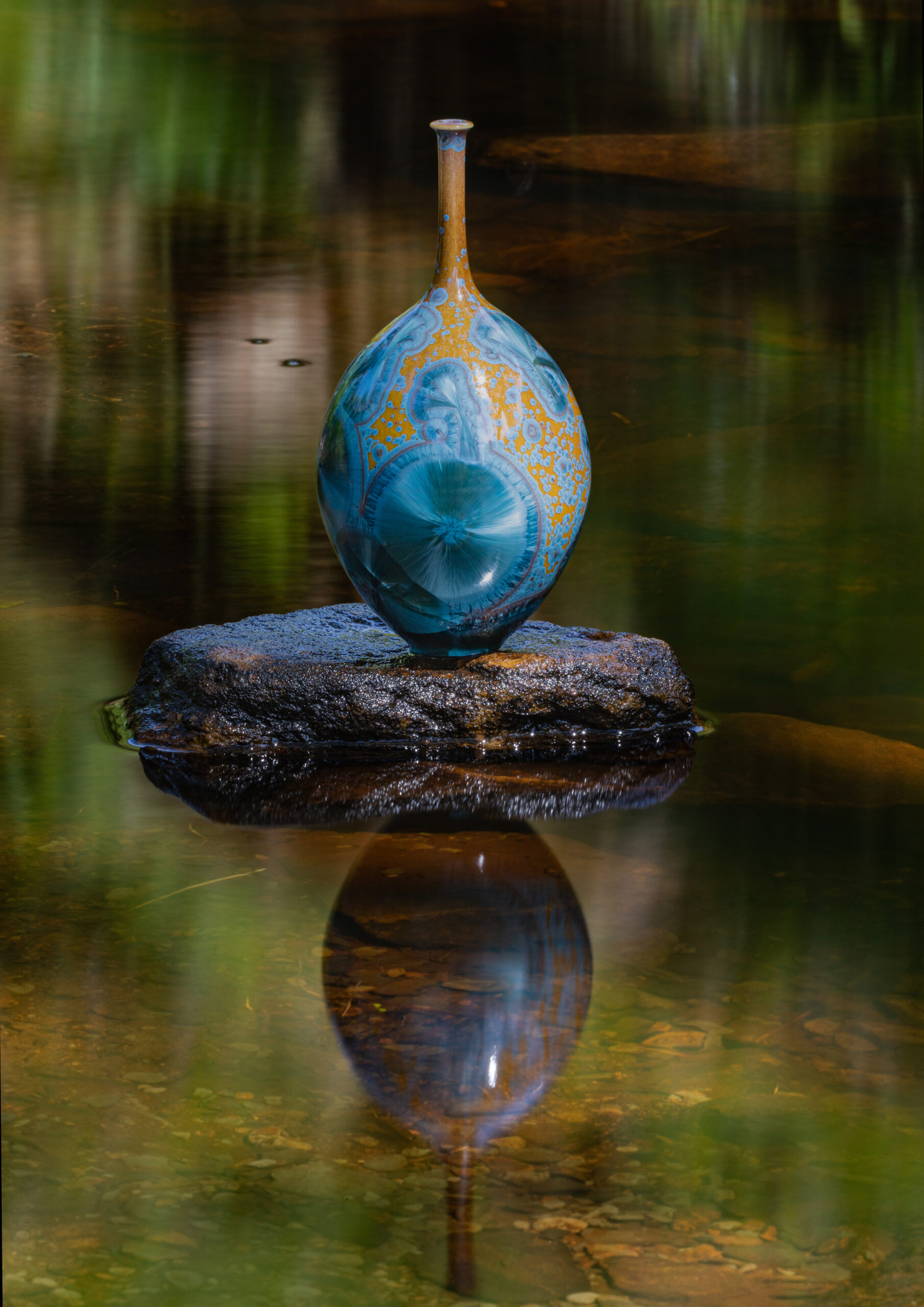
CGC reflected in a pool of water. 2022.
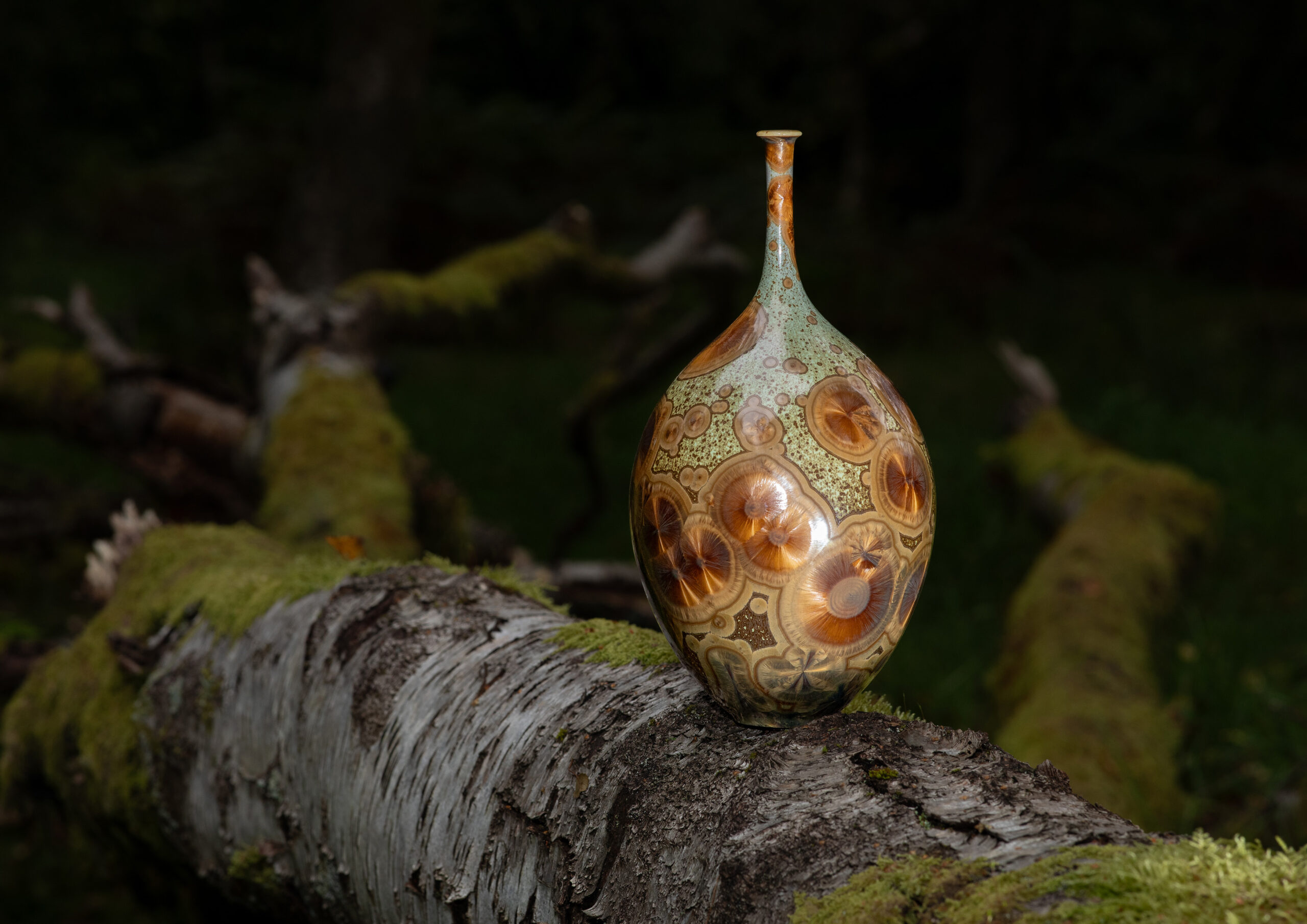
CRK pictured on a fallen birch tree. 2023.
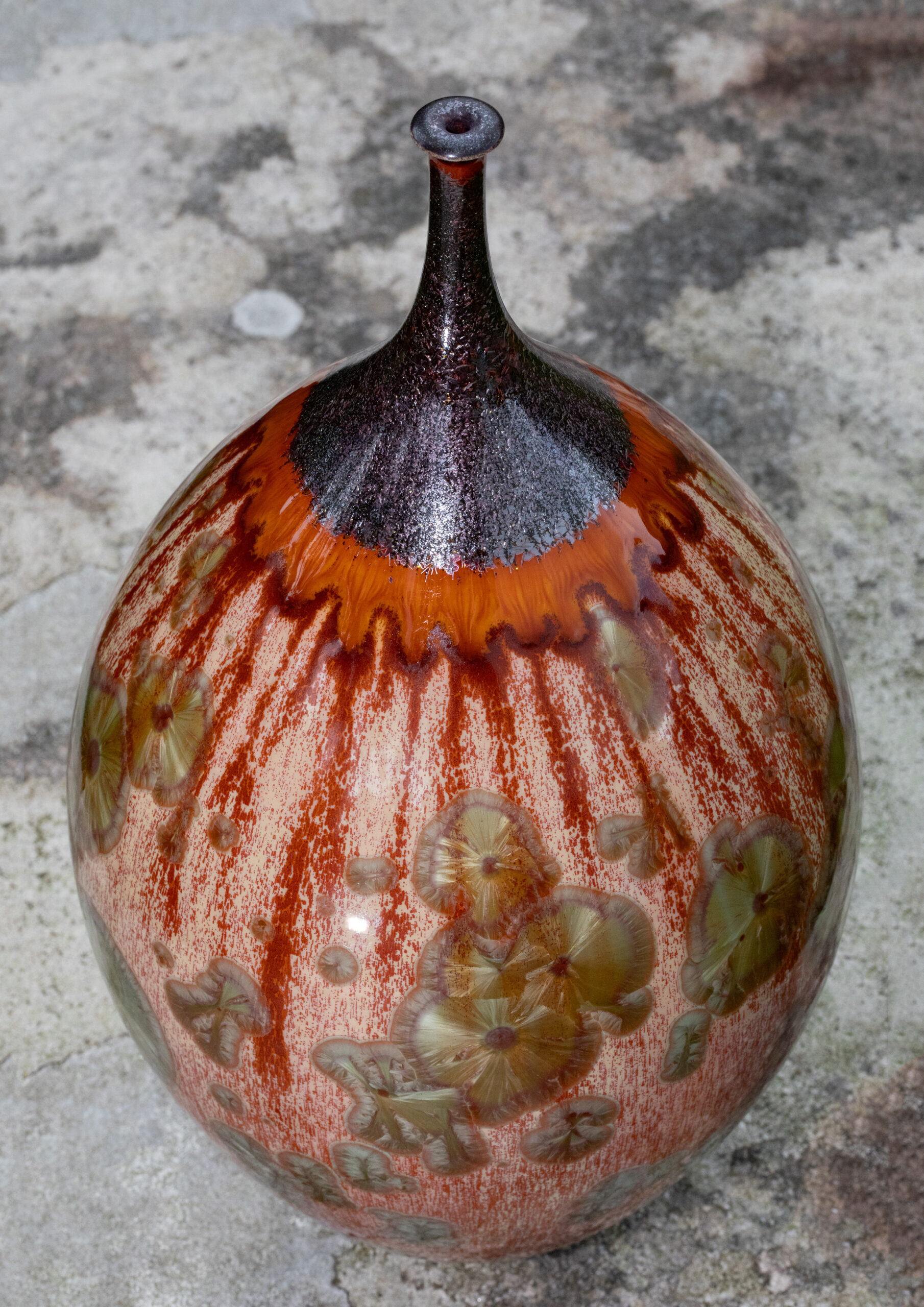
CWJ pictured in the grounds of Hutton-in-the-Forest during Potfest in the Park 2024.
Plain Backdrop Images
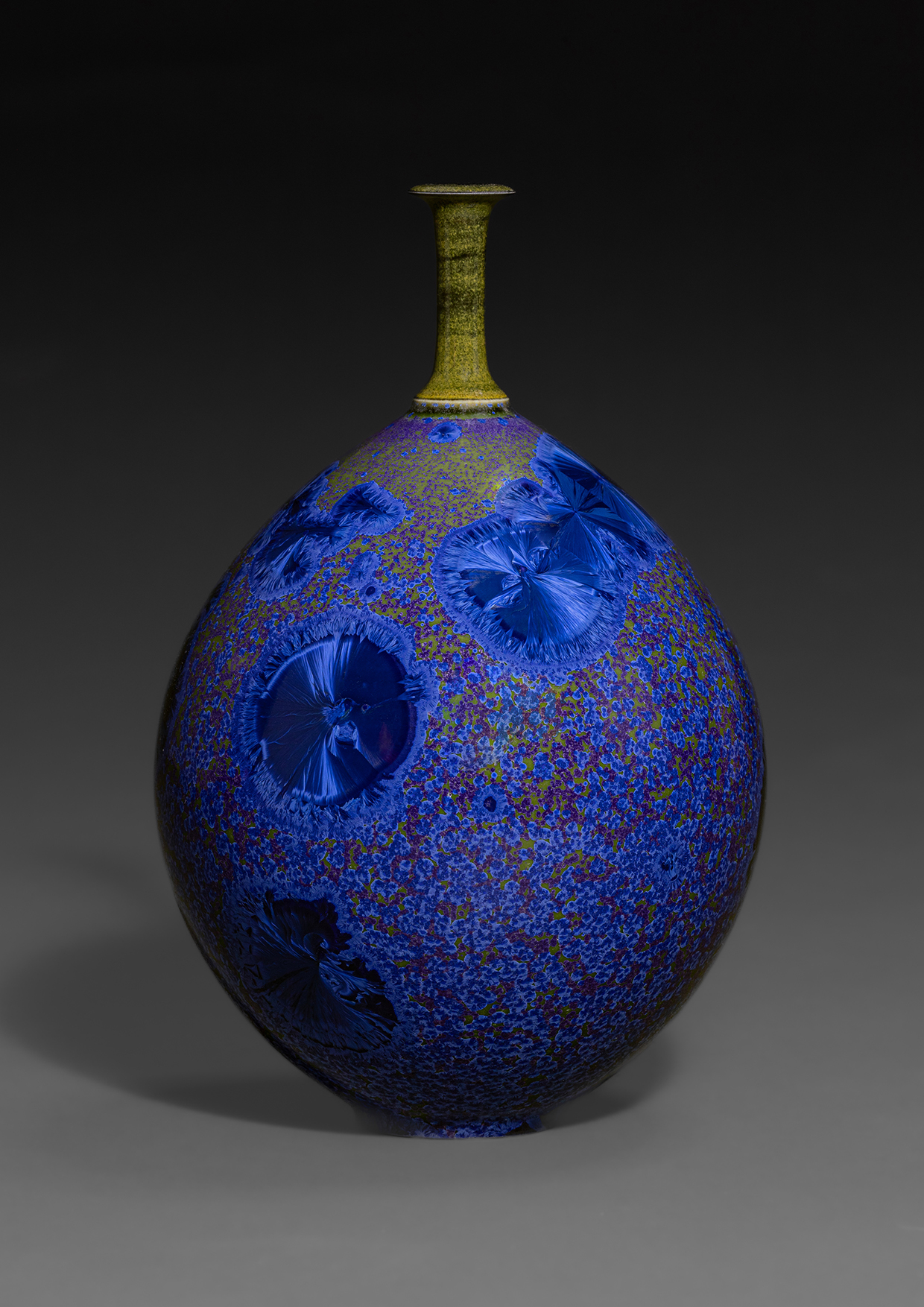
CU9. Iron khaki on the neck, mid blue and purple crystalline on the body. 205mm tall, Royale porcelain.
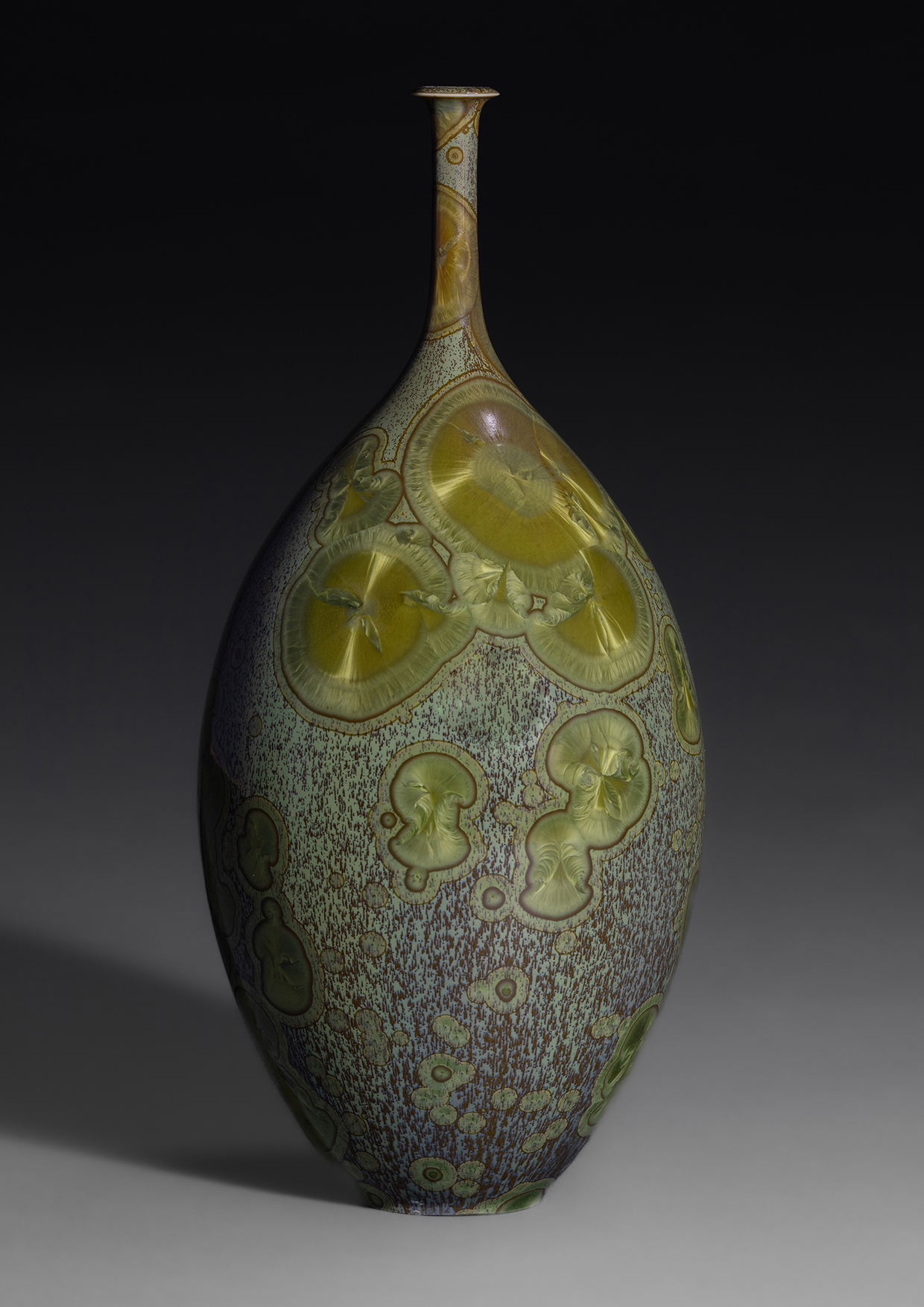
CWE. Pale green and gold crystalline glaze. 250mm tall, Richard Bideau custom porcelain number 89.
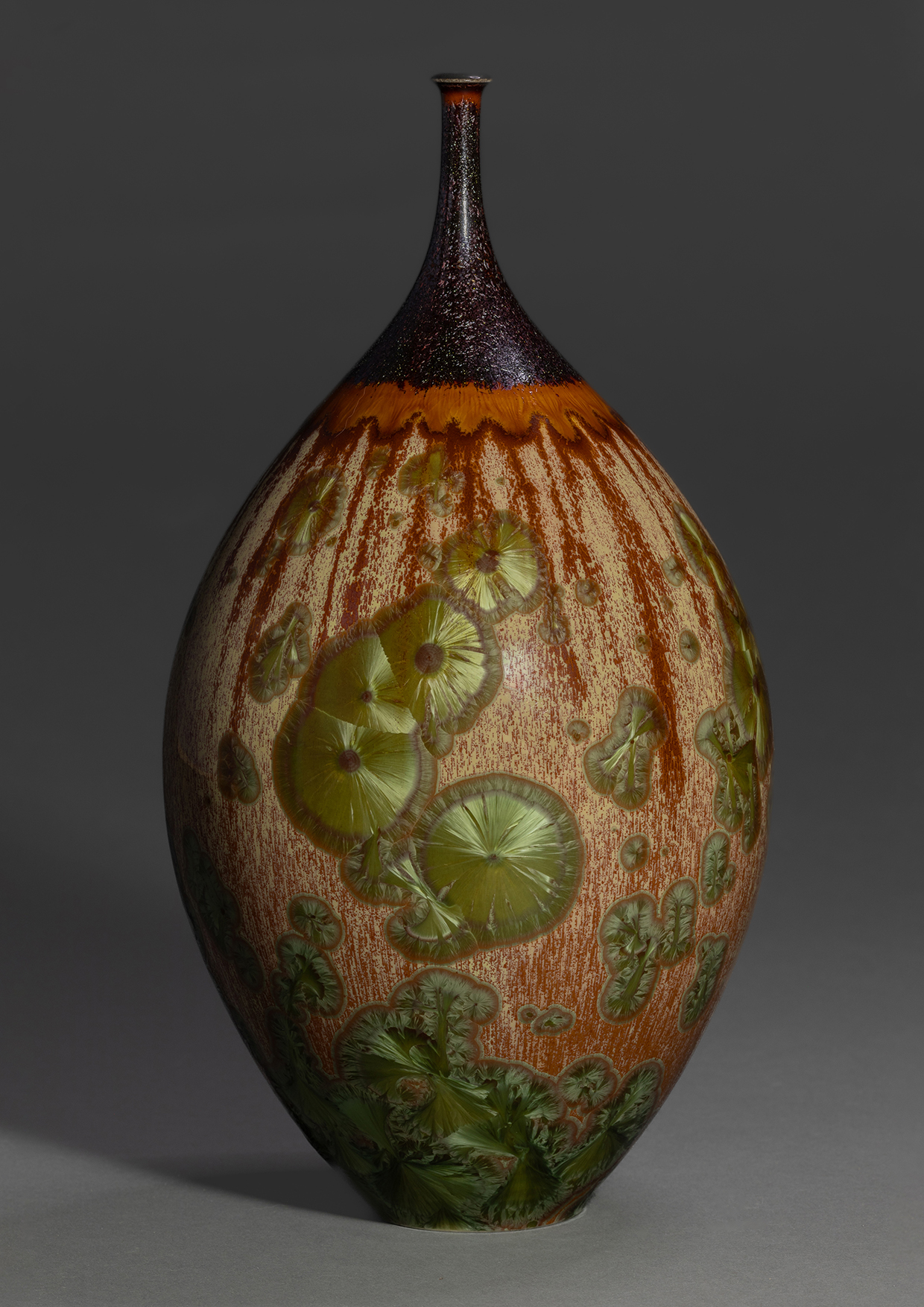
CWJ. Iron aventurine on the neck> Emerald green crystalline glaze on the body. 300mm tall, Richard Bideau custom porcelain number 92.
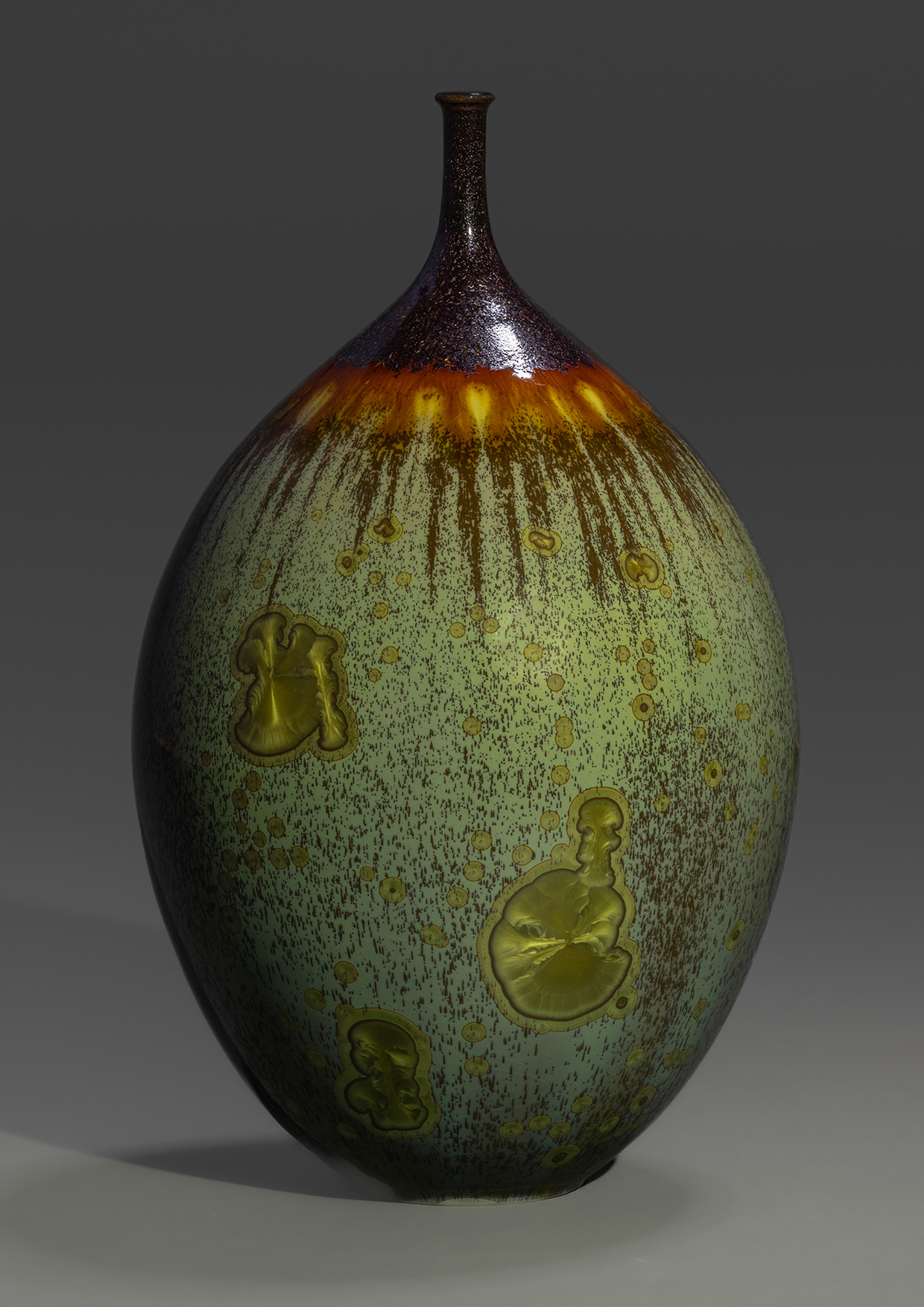
CWL. Iron aventurine on the neck. Pale green and gold crystalline glaze on the body. 270mm tall, Richard Bideau custom porcelain numnber 92.

CWU. Iron aventurine on the neck. Emerald green crystalline on the body. 305mm tall, Richard Bideau custom porcelain number 95.
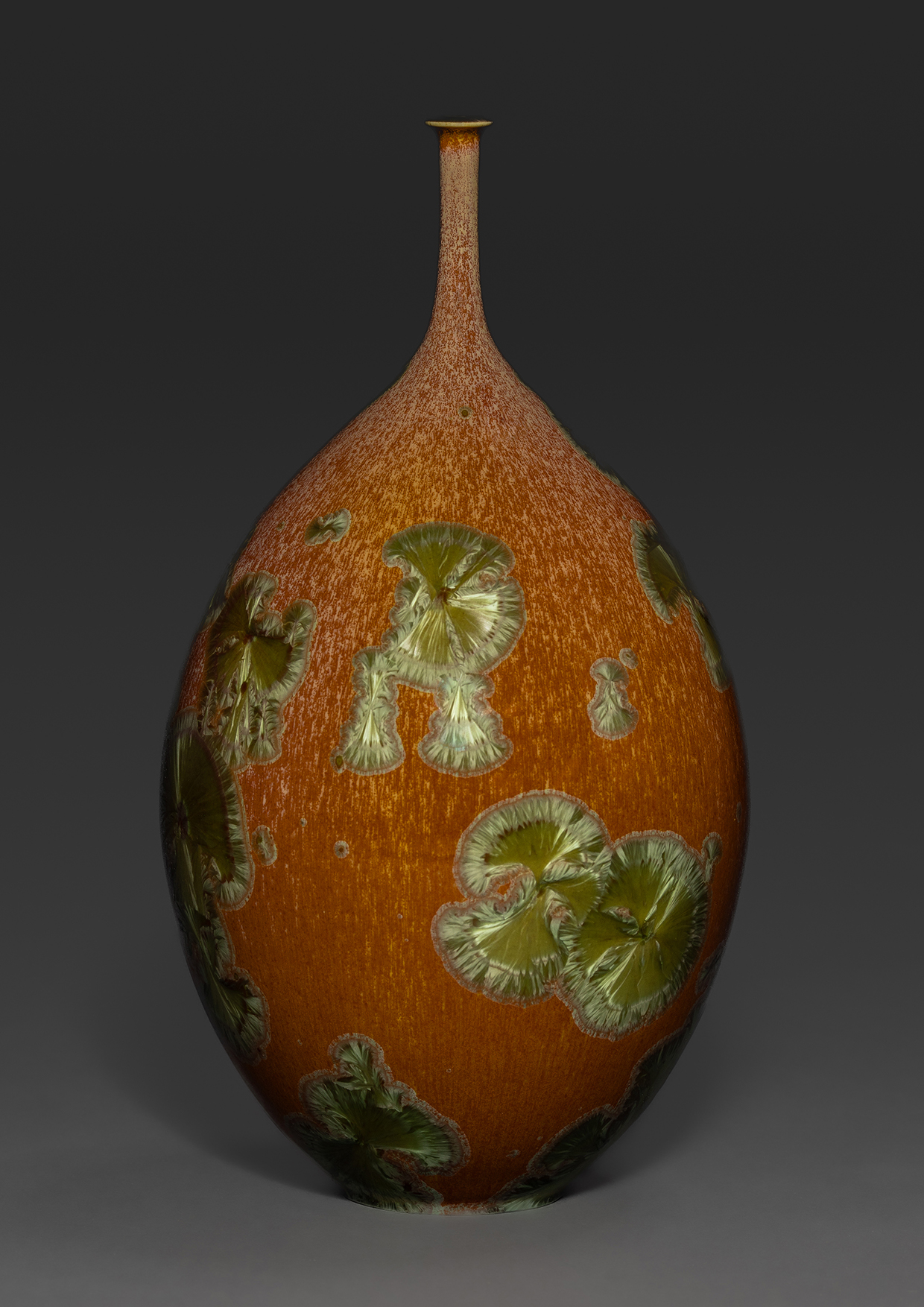
CWV. Emerald green crystals on a tan ground. 215mm tall, Richard Bideau custom porcelain number 95.
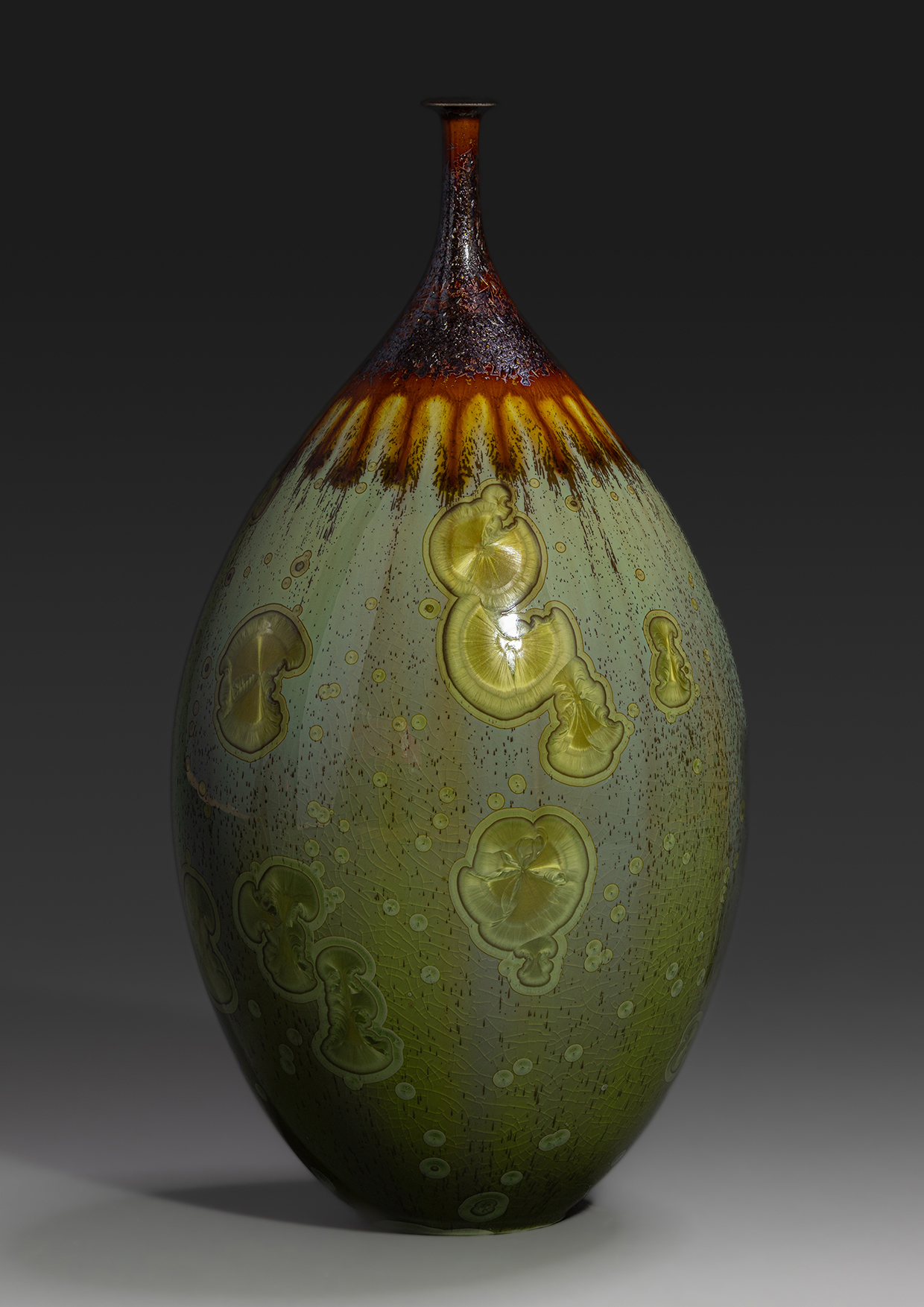
CWX. Iron aventurine on the neck. Pale green and gold crystalline on the body. 315mm tall, Richard Bideau custom porcelain number 92.
Information
Based in Lancashire in the north of England, I sell my work at exhibitions and through galleries in the UK. All of my work is done in my custom-built workshop close to my house.
I designed my 7ft3 (200 litre) front loading electric kiln and its controller specifically for the demands that the crystalline process places on firing. There are three independent zones, each with thermocouple and element bank, that are individually controlled to achieve temperature uniformity throughout the firing chamber. The controller has the capability of a practically unlimited number of firing segments, allowing complex temperature profiles to be achieved. The vents that let air into the kiln for cooling are motorised and linked to the controller.
My preferred type of clay body is porcelain and for many years I have used the popular Audrey Blackman body made by Valentine Clays in Stoke-on-Trent, England. I also make my own porcelain bodies and recently I have moved towards a formulation of my own that gives especially good results with my glazes and stands up on the wheel better than Audrey Blackman.
Over the years I have become frustrated with variability of frits, especially Ferro 3110. I have solved this problem by making my own. A side benefit is that, because my frits have no alumina in them, I can incorporate a useful amount of kaolin into my recipes allowing for better glaze rheology and application characteristics.
My favourite glaze has its origins in a series of tests I performed in the year 2009. It has many variants, achieved through small changes to the chemistry and most of which produce an abundance of different secondary crystals depending on the firing cycle and porcelain body composition. It works very well in combination with my iron silicate aventurine glazes. While it can not be realised exactly with commercial frits, a close approximation is:
Ferro 3110 frit 24.0
Ferro 3195 frit 3.5
calcium carbonate 2.6
barium carbonate 8.2
zinc oxide 28.4
kaolin (grolleg) 3.2
silica 30.1
+titanium dioxide 1.0
+red iron oxide 4.0
+cobalt oxide 0 – 0.7
All are by weight. Varying the amount of cobalt oxide changes the colour from pale honey (no cobalt) through to very delicate green crystals on a honey ground (0.05%) through to blue crystals on a blue ground (0.7%). I prefer the amount of cobalt that produces a subtle green.
A good firing cycle for this glaze is:
1) as fast as my kiln allows until 1185°C (2165°F)
2) controlled heating at 60°C/h to 1285°C (140°F/h to 2340°F)
3) about 5min hold at the top temperature but varied from recent firing experience to ensure Orton cone 10 is down by the end of the firing.
4) 5 cycles of cooling to 1050°C followed by heating to 1080°C all at maximum rate (1922°F and 1976°F).
5) 2 hours hold at 1140°C (2084°F) for primary crystal growth
6) 0.5 hours at 1000°C (1832°F) for secondary growth and primary fringe development.
My background in chemistry that first drew me to crystalline glazes. The first time I saw them I was fascinated by the possibilities that these sparkling surfaces offered. Starting from a recipe published by Derek Clarkson, I have experimented and developed thousands of glaze variants over a time spanning nearly 30 years. Gradually, I have moved away from the more vivid glazes and settled on a style that adds the texture of secondary crystals to the usual zinc silicate primaries. I aim to capture some of the features of nature: lichen on an old wall, minerals glittering in rocks, flowers on a sun-dappled woodland to name but a few. The backdrops I choose for photography are all chosen from the local landscape.
Aventurine Glazes
The four aventurine image here are all 1:1 macro shots on a 35mm frame, the extent of each is approximately 24mm x 36mm on the glazed surface. Static images cannot convey the complexity of these glazes wich shimmer and sparkle as light hits them.
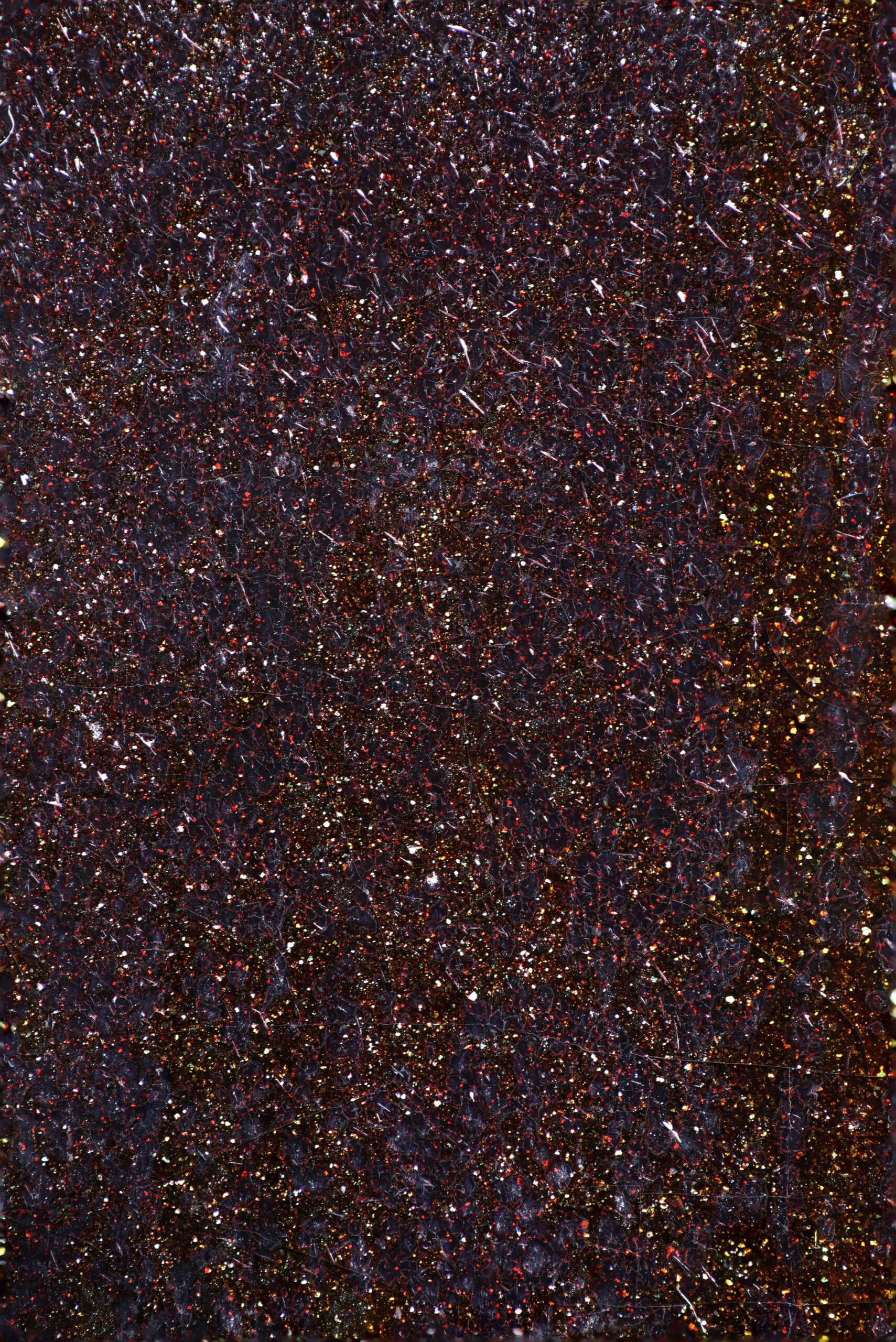
9096 produces very small crystals that sparkle as light hits them.
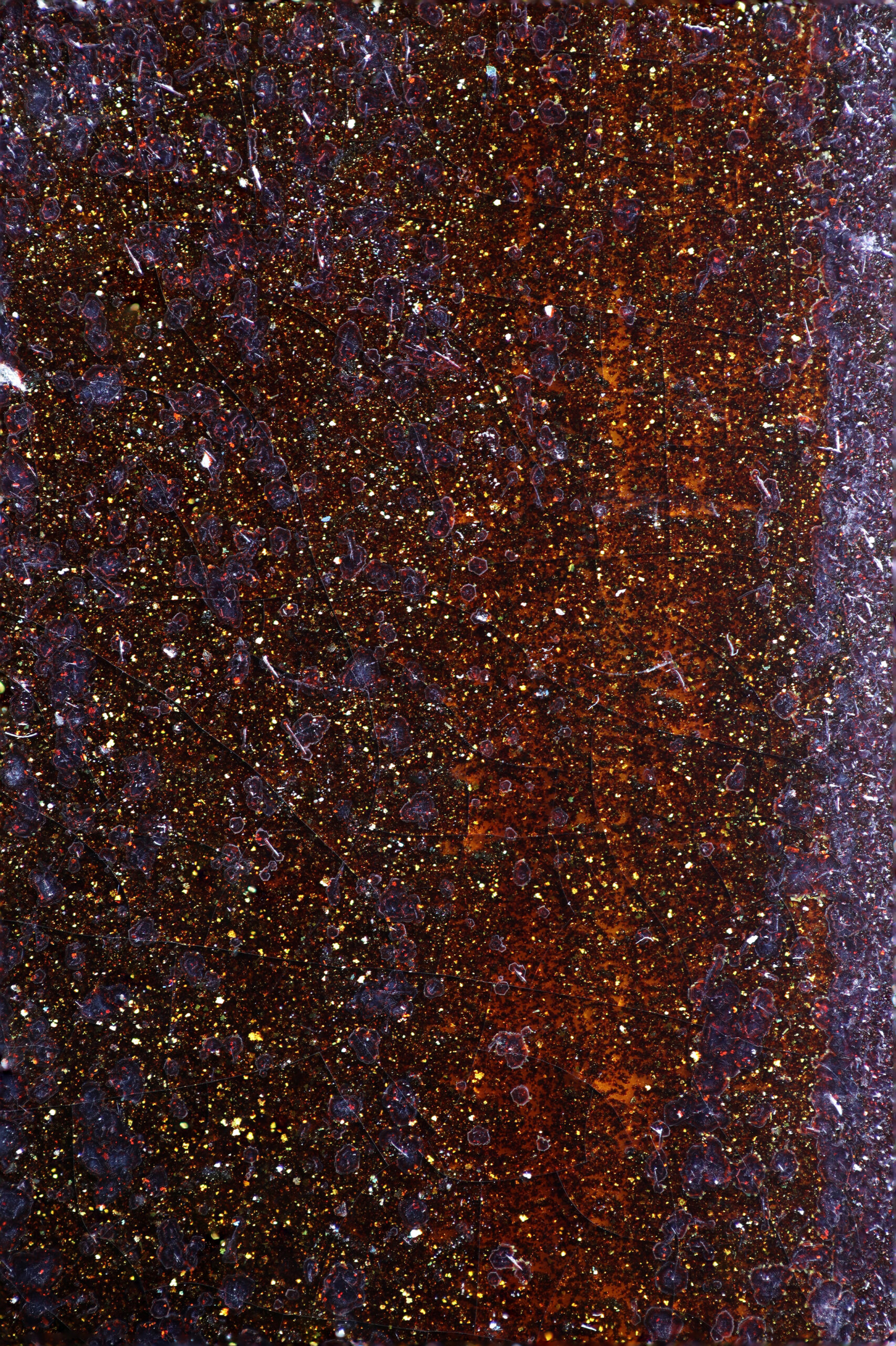
9138 is similar to 9096.
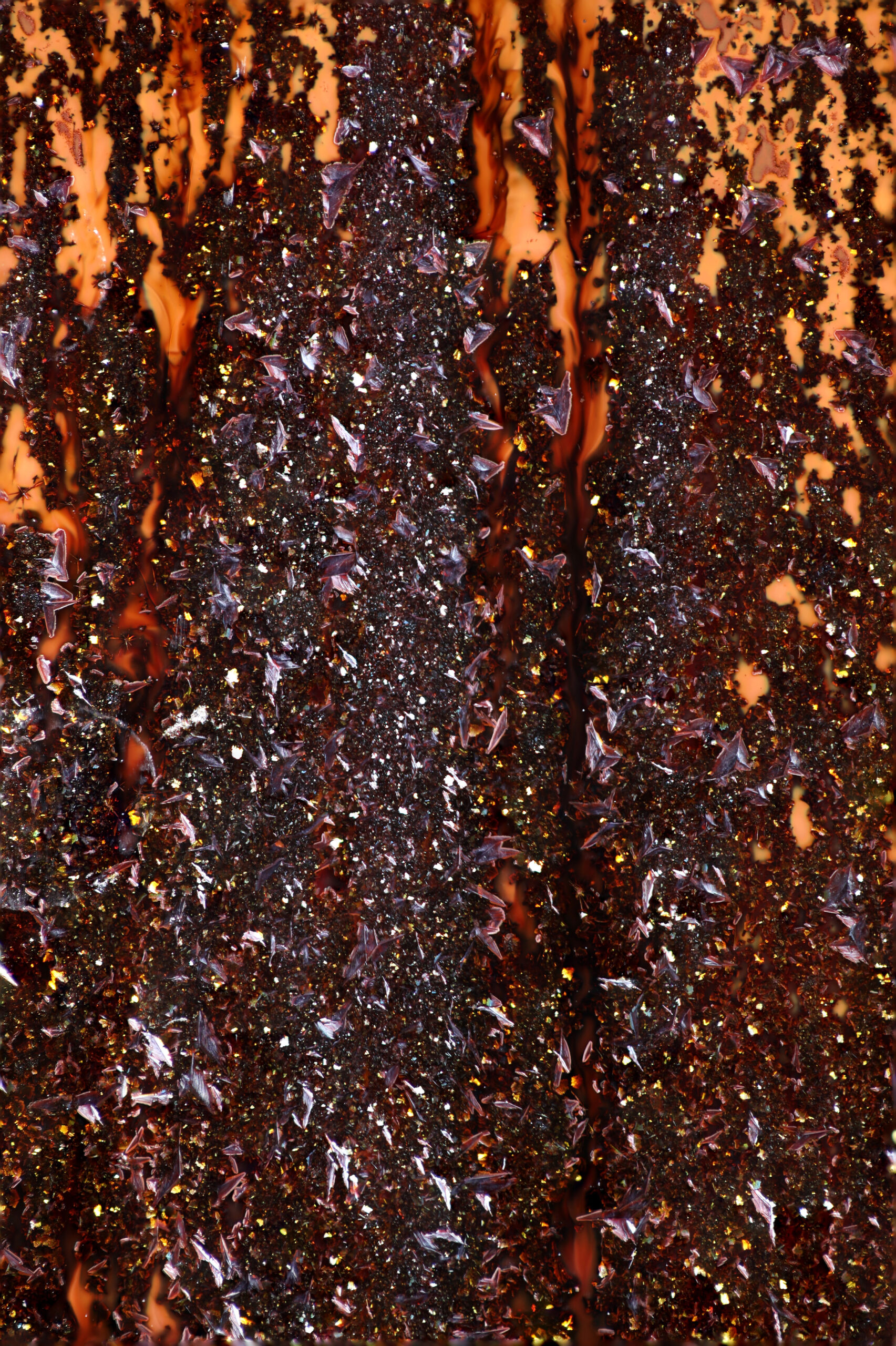
9152 adds larger crystals to the small all embedded in a semi-opaque ground.
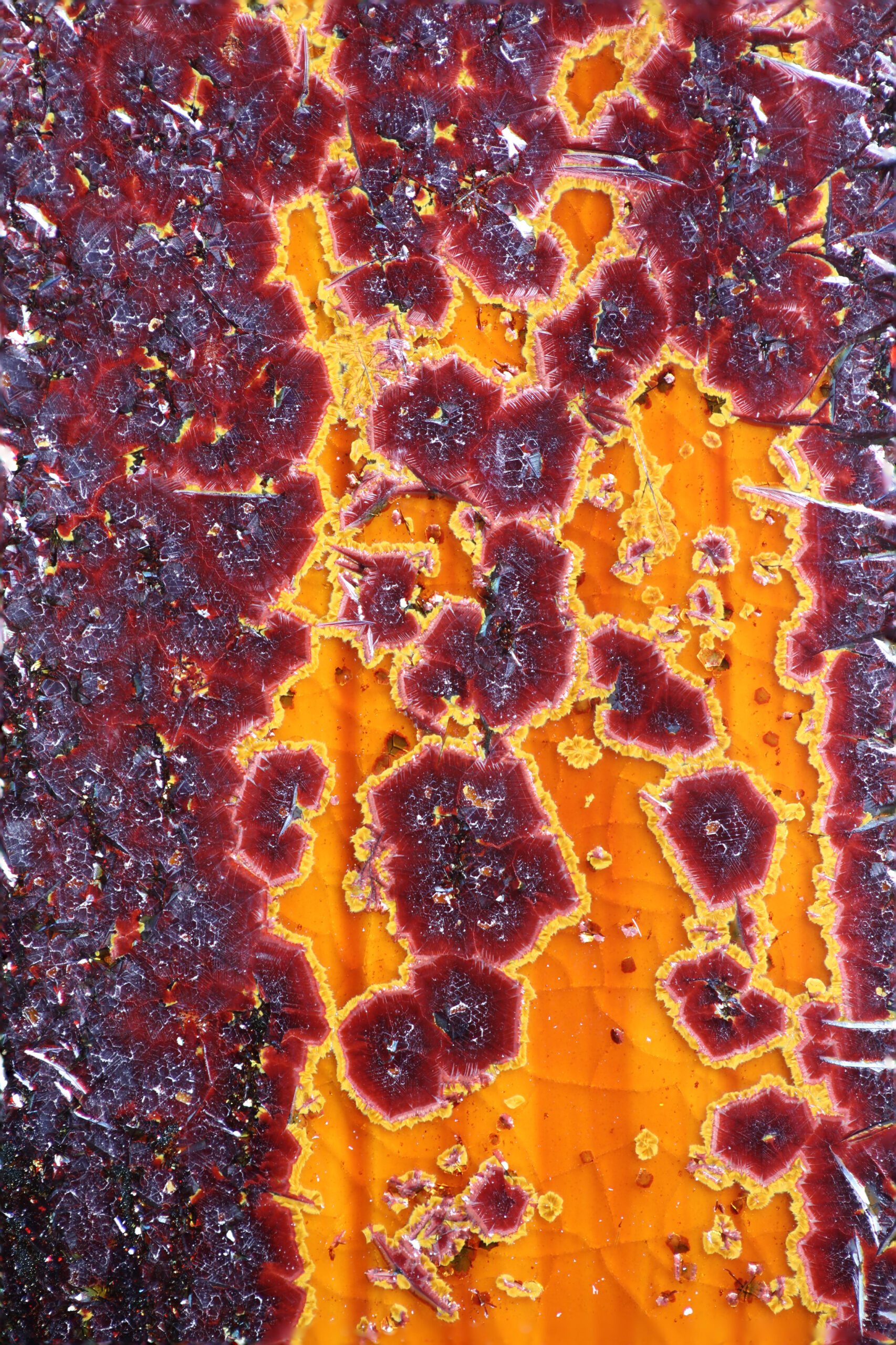
With 9276 larger crystals dominate, the small glittering crystals are largely absent. The biggest crystals here are approximately 4mm across.
Preliminary Material
The sample images on this page are all available in A4 size, 300 dpi with pixel dimensions 3508 x 2480. Two of my pieces are featured: CR1 and CVR together with macro shots of the secondary crystals for each glaze type. The zinc silicate crystalline glazes on these two pieces differ only in the amount of cobalt oxide. CR1 has about 0.7% giving a strong blue, CVR has around 0.1%, enough to give a green tinge to the primary crystale but not enough to overcome the amber and tan tones from iron oxide. This glaze gives an exceptionally strong development of secondary crystals.
CR1
CR1 is a thrown and turned porcelain bottle form featuring my dark blue zinc silicate crystalline glaze in conjunction with a tea dust glaze on the neck. This particular glaze in conjunction with my custom porcelain body formulation number 69 develops an especially rich variety of secondary crystals. The macro shots show the complexity of the secondary development.
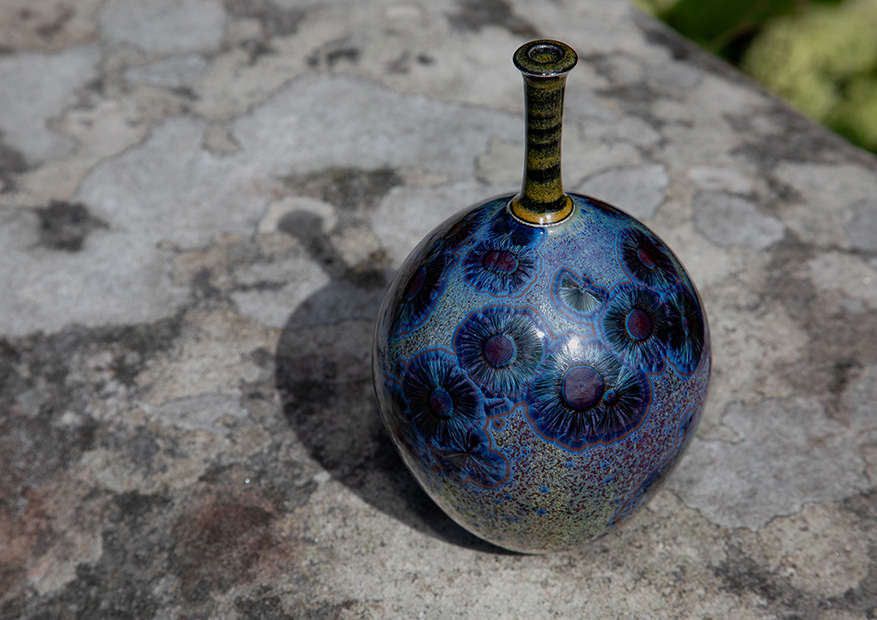
CR1 in bright sunlight with flash fill, taken at Hutton-in-the-Forest during Potfest in the Park 2023.
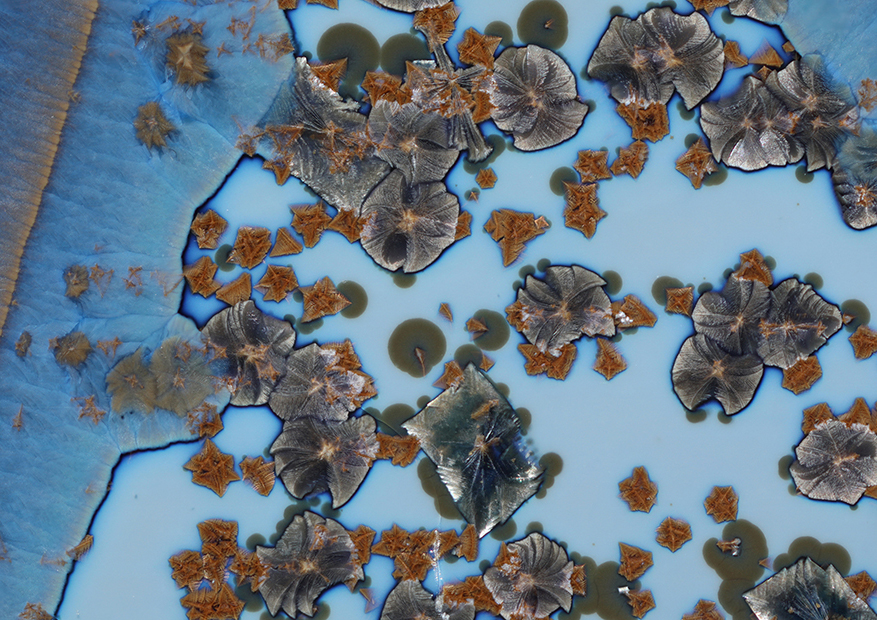
Magnified view of the secondary crystals. The region shown here is 7mm x 5mm in size.
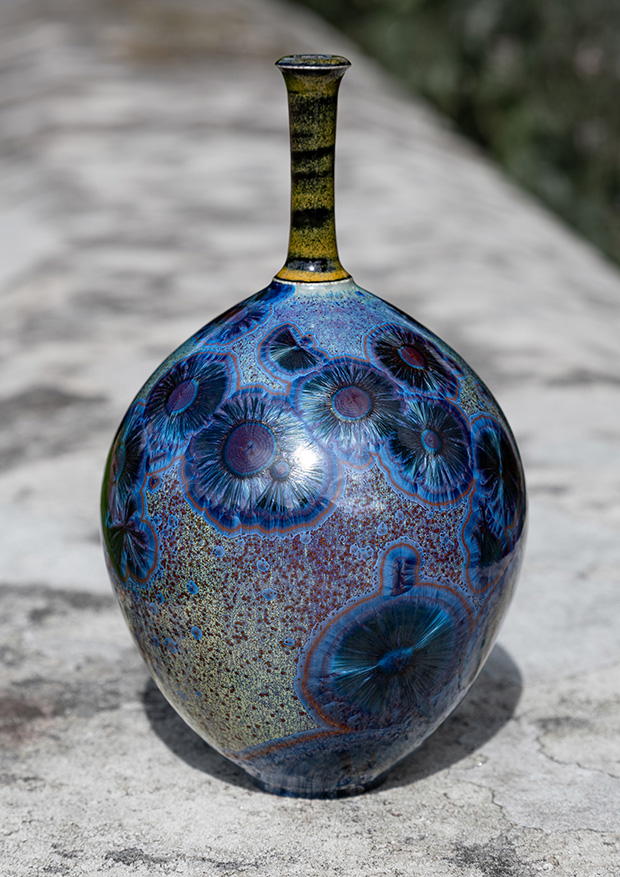
Another view of CR1, bright sunlight with flash fill.
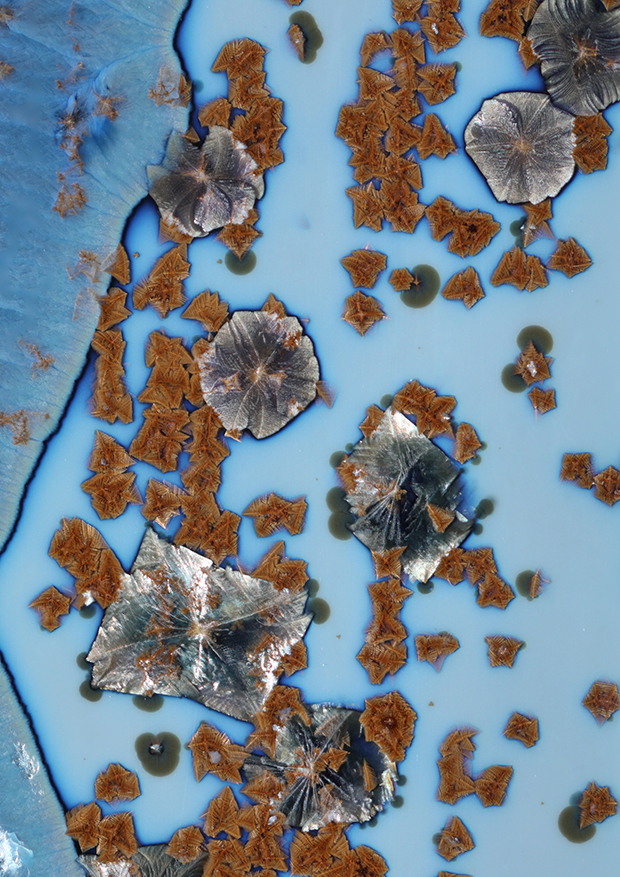
Magnified view of the secondary crystals. The region shown here is 4.7mm x 3.3mm in size.
CRV
This thrown and turned bottle form is made from a commercially available body: Royale Porcelain made by Valentine clays. The top of the piece is glazed with one of my favorite iron silicate crystalline glazes. I have carefully adjusted the fluidity of this glaze to create a vivid pattern where ot meets the zinc silicate glaze on the body. The pattern arises spontaneously in the firing.
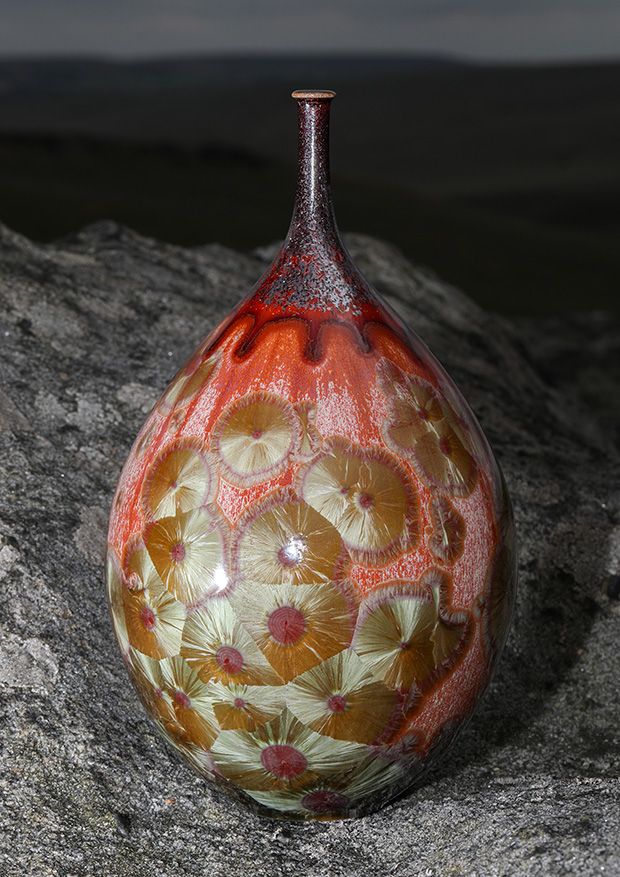
CVR pictured on an outcrop of gritstone in the uplands of Northern England.
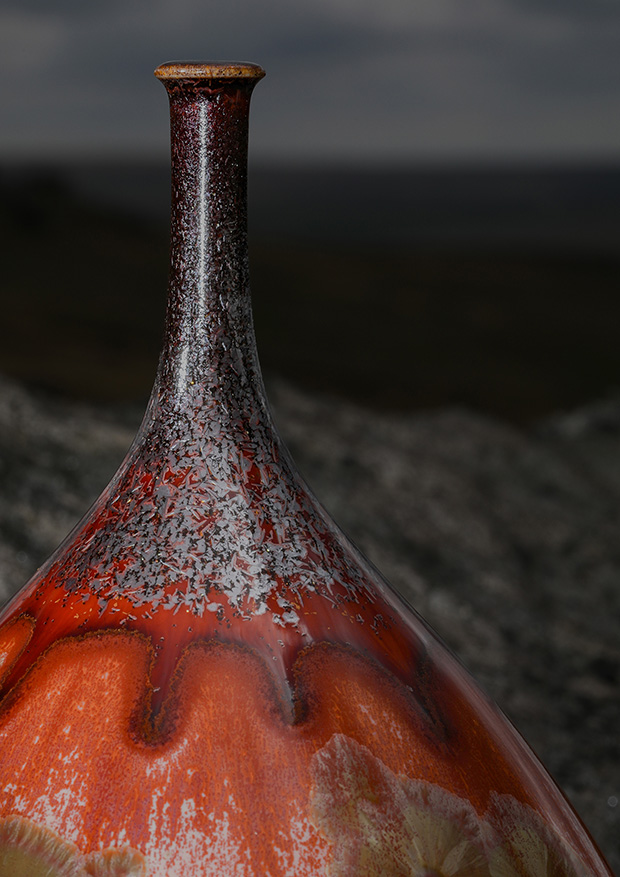
Detail of the iron silicate glaze on the neck.
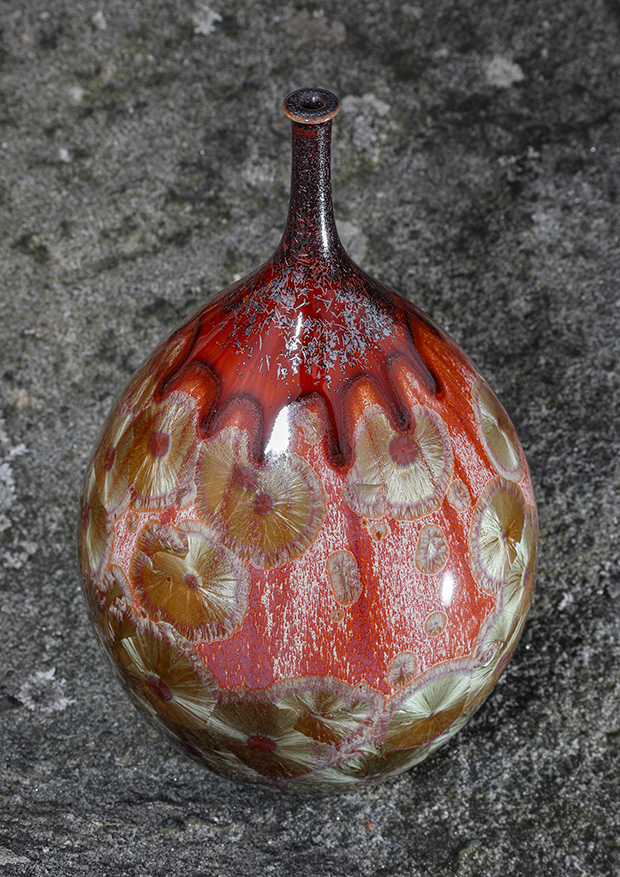
Detail showing the interaction between the two glazes.
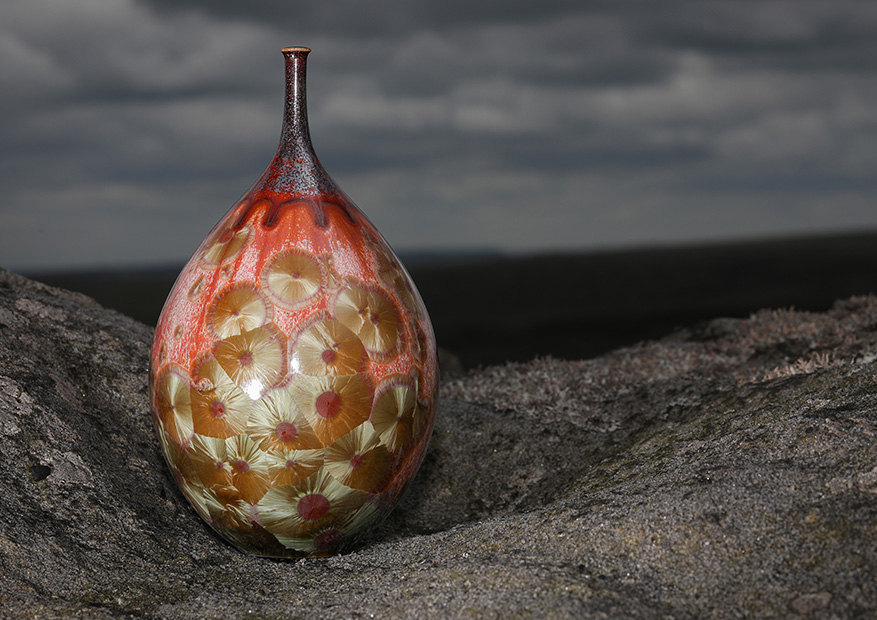
CVR pictured on an outcrop of gritstone in the uplands of Northern England.
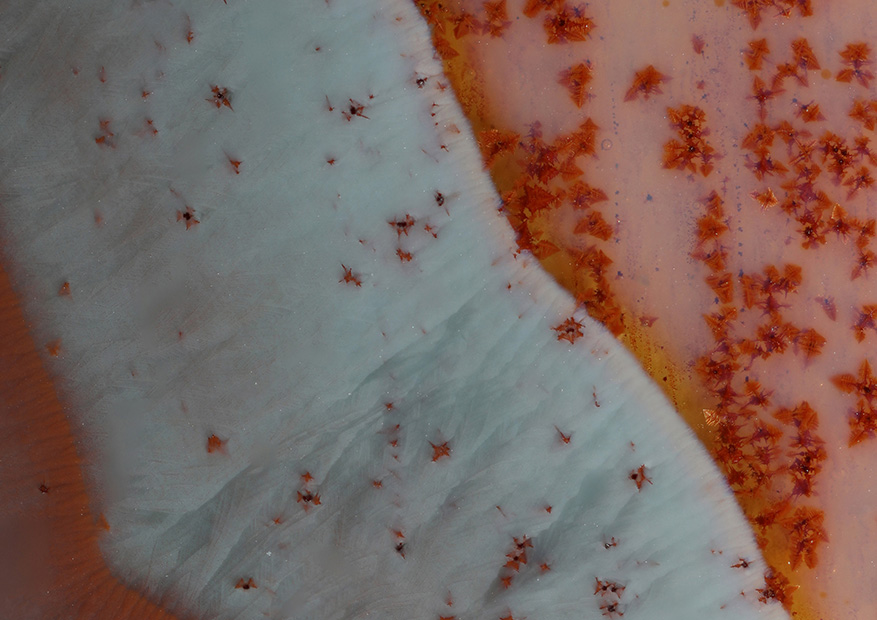
Magnified view of the secondary crystals. The region shown here is 3.2mm x 2.3mm in size.
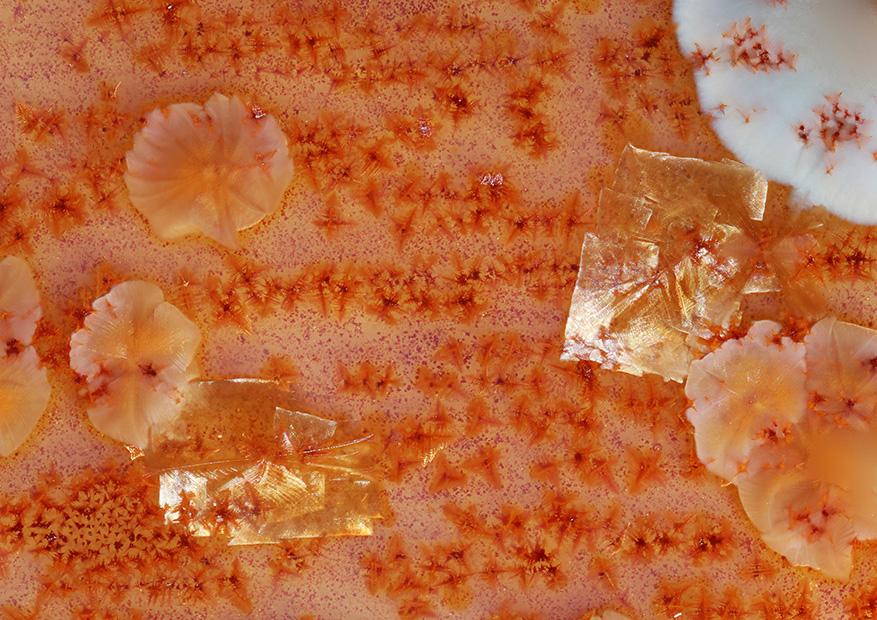
Magnified view of the secondary crystals. The region shown here is 3.8mm x 2.7mm in size.