With crystalline effects, the glaze is only a part of the process. The type of clay body also exerts a powerful influence on the fired result. For this reason, and many more besides, each potter, working in different parts of the world, each with its own raw materials, produces effects that are unique.
My research into porcelain body formulation was initially to formulate a body that performed better on the wheel than commercially available porcelains. That I have achieved, but in addition, it has given me a appreciation of just how significant a contribution the porcelain makes. Here I describe a body made in part from materials local to my workshop. I am fortunate that the surrounding geology contains many clays from the Carboniferous Period.
Geological Setting
During the late Carboniferous, what is now the north of England, was located close to the equator. A huge river, heavy with sediments eroded from mountains to the north, drained lazily into a shallow sea across a delta that spanned hundreds of square miles. Over millions of years, the sea and land levels changed cyclically. During times of innundation, the shallow sea bed was covered in sediment brought by the river. When dry land, huge swamps formed, heavy with vegetation. Over time the sediments were buried and compressed. Those composed of clay minerals became mudstones and shales, the organic matter became coal and the soils upon which the plants grew became fire clays, also known as seatearths.
At this location, high up on the moorland at the border between Lancashire and Yorkshire, these sediments are cut through and exposed by a small stream. Marine shale, seatearth and coal are all displayed.
Seatearth
This is the seatearth of the coal known locally as the Lower Mountain Mine. The grey material next to the hammer is smooth textured and very plastic. This clay occurs in many locations in the Lancashire coal field. In the past, when the coal mines were active, it was used for the production of high quality fire bricks. Alone, it fires to a pale buff colour at cone 10, remaining unvitrified. The sequence here suggests movement after deposition, there is no coal above, instead a sequence of shales, the seatearth may be an isolated raft detatched from the main sequence.
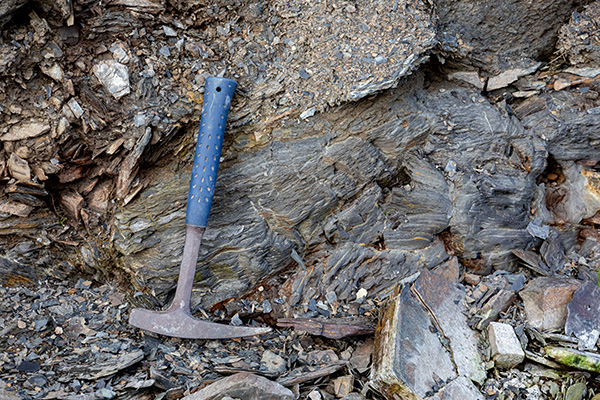
Lower Mountain Mine
In Lancashire coal seams are referred to as ‘mines’. This is the coal of the Lower Mountain Mine sat upon the seatearth and grading upward into the marine shales at the top of the hammer.
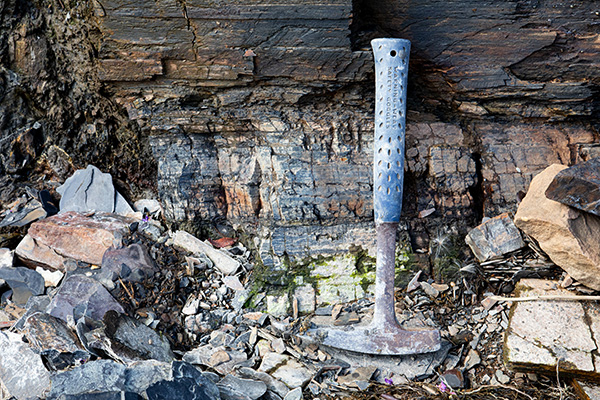
Marine Shale
On the right in the picture a half-meter sequence of marine shale is exposed. The sequence continues upward for several more meters forming an unstable cliff that continually showers the stream bed with tiny rock fragments. The shale is soft and cleaves easily revealing fossils on the bedding planes. This is the Gastrioceras listeri Marine Band, so called becuase of the presence of an ammonite of that name. Shales like these are often the basis of ordinary building bricks. The famous Accrington brick (back in production at the time of writing) is made from a similar shale. It occurs in a different sequence to this one, slightly younger but still from the Carboniferous.
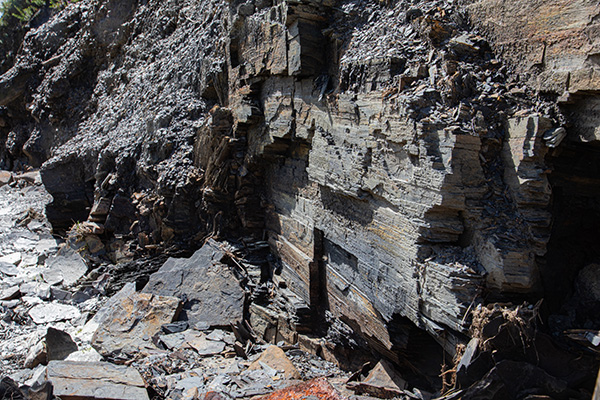
Fossils in the Marine Shale
The fossils are poorly preserved but the spiral formations of ammonites and the occasional shell of bivalve mollusks can be found.
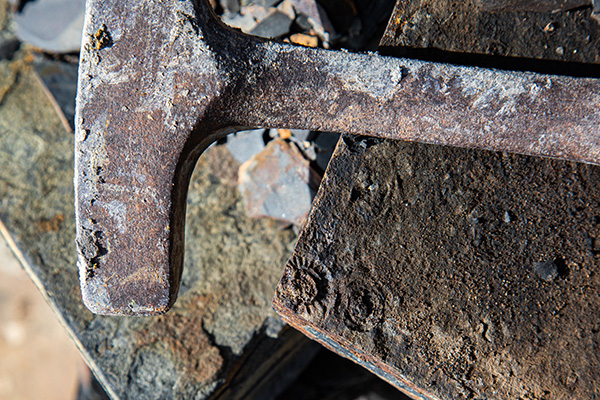
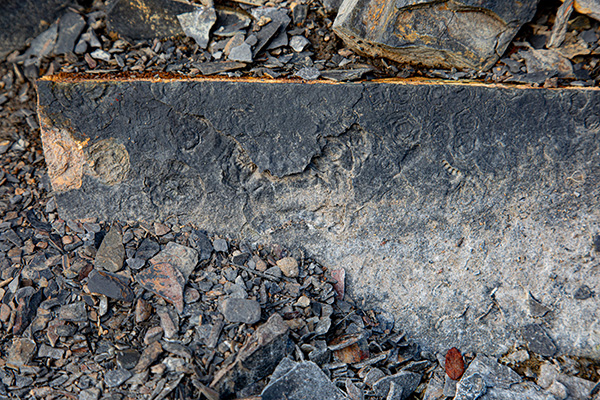
Formulating a Porcelain
My custom porcelain throwing bodies are variations on the conventional triaxial formulation, so called because they are made from three ingedients: feldspar, clay and silica. The clay I divide between china clay and ball clay, varying the types of each to give the properties I want. I use the sliphouse method: to the powdered ingredients, sufficient water is added to give a fluid slip, thoroughly mixed by a powerful paddle mixer, flocculated, sieved through 200s mesh and then dewatered on a plaster bat. This method gives me an extremely plastic body that does not need prolonged ageing, it is ready to use in a matter of days.
I have found that the crystals in my glazes change depending on the body formulation, most particularly the nature of the ball clay used. Of the materials in a porcelain, ball clays are the most variable. They are more complex than the relatively pure kaolins provided by the china clay because they contain many more types of mineral. Testing a new ball clay is always exciting.
In this case, I simply substituted the ball clay for the Lower Mountain Mine seatearth, refined first by sieving through 400s mesh and then drying to a powder. The resulting porcelain body is grey in the raw state due mainly to organic matter in the seatearth. It fires to an off-white ivory giving a degree of vitrification very similar to my more conventional porcelains. The crystalline result is different. I made a small number of pieces with this clay and all, when compared with the same glaze on other porcelains, are exceptional for the complex primary and secondary crystal development. Colour too is a little different, iron from the seatearth tends to make the ground darker. Unexpected was the result on the primary crystals: the colours are a complex shade of green and blue.
The marine shale is also a possibe ingredient. Shales like this one are relatively non-plastic but gradually form clay like bodies after weathering. A sample that I prepared by ball milling for 24 hours did become extremely plastc. I have a larger sample slowly ageing in water, I’m hoping that will produce a more plastic material suitable for a future experiment.
Examples
CRH
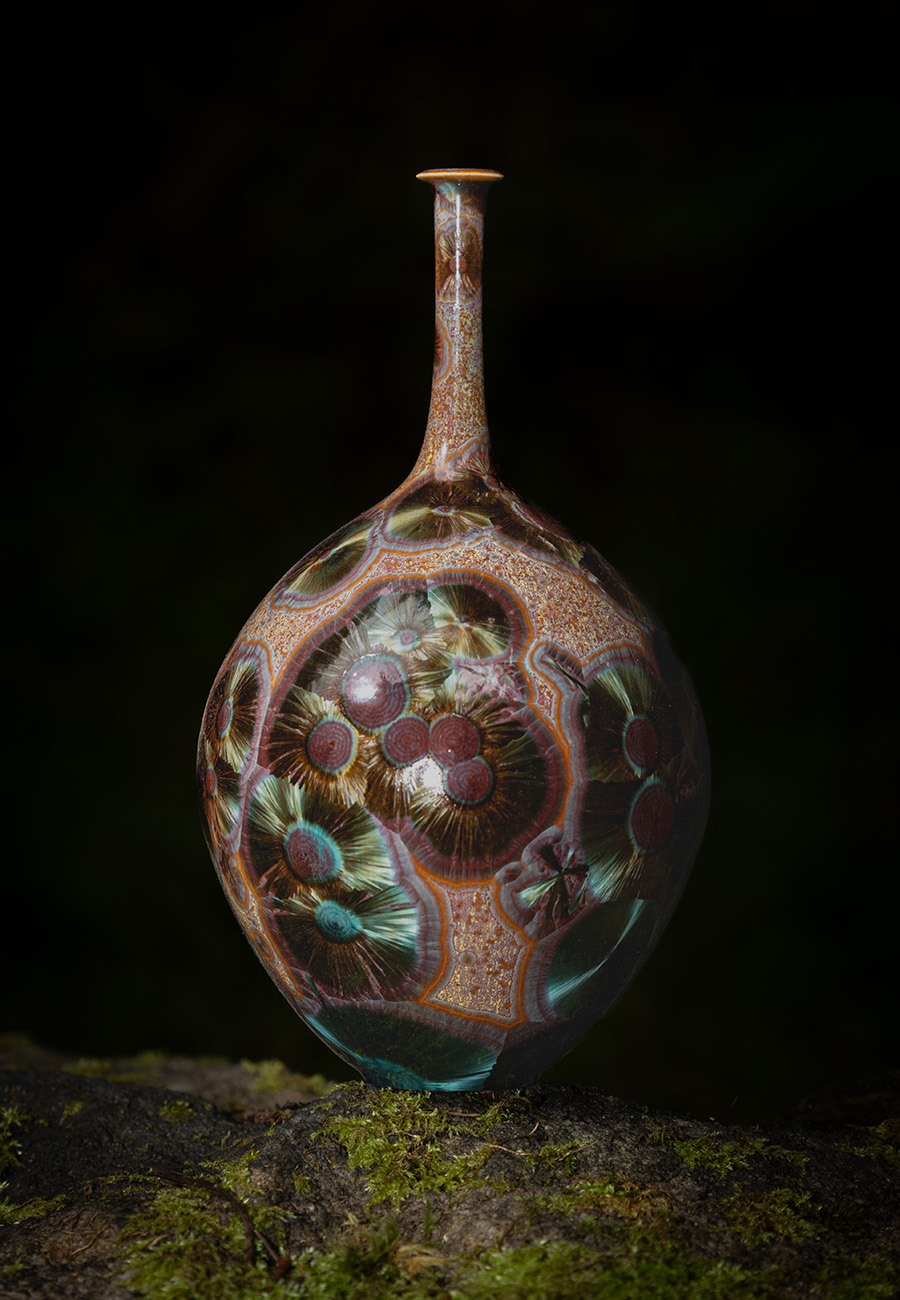
CP5
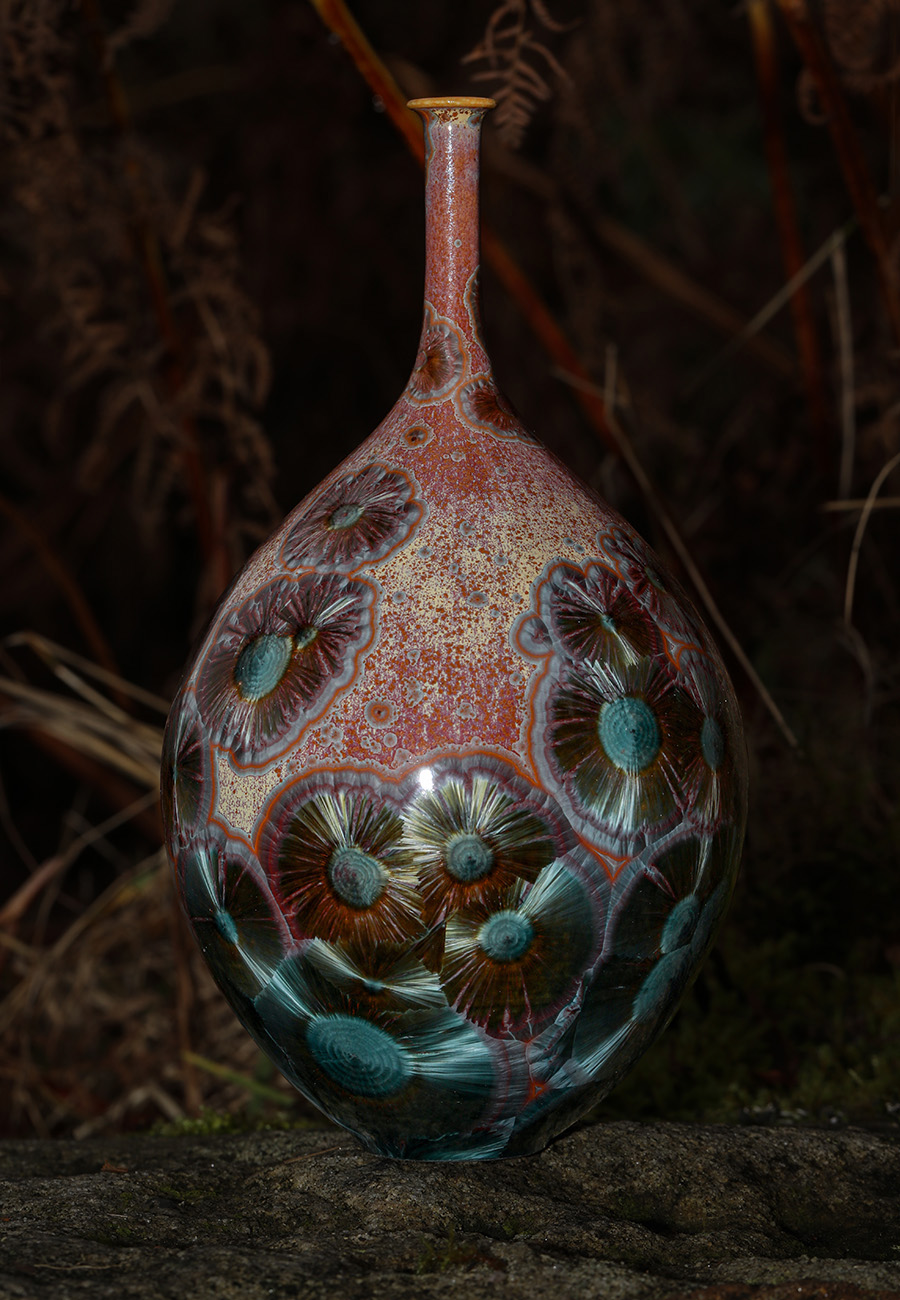