Cups need to withstand the thermal shock of having hot liquid poured in over and over again. This places several requirements on the clay body and glaze coating, one of which is the need for the internal glaze and body to have compatible thermal expansion characteristics. A common failure is caused by having an internal glaze with a thermal expansion coefficient lower than that of the body, a cup made with this problem will often fail when hot liquid is poured in. As the cup cools in the glaze firing a point is reached where the clay body and glaze start to behave as solids and can no longer deform plastically under the influence of heat. As they cool further, each contacts according to its own thermal expansion coefficient, a property largely determined by composition. If expansions are matched, no stresses develop between body and glaze. If however, the glaze has a lower expansion coefficient, it shrinks less and the body is placed in tension by being stretched over the glaze. When hot liquid is poured in, the glaze experiences a change in temperature before the body because it takes time for the heat to flow outwards. This causes the glaze to expand thermally first, placing a tensile stress on the body. If the body is already in tension because of a coefficient mismatch this additional stress can be enough to break the body – the cup fails, often with a loud ‘ping’. Here I present a simple method for testing the internal glaze.
Thermal Shock Bottles
The test pieces are in the form of a flat-bottomed round bottle, 50mm in diameter, slipcast in a simple two-part mould. I make thin walled casts giving a wall thickness of around 1mm (5 minutes typical casting time). The size makes it convenient for glazing on the inside with 10ml of glaze slip. Glazing is simple: pour in, shake for a few seconds and then drain.
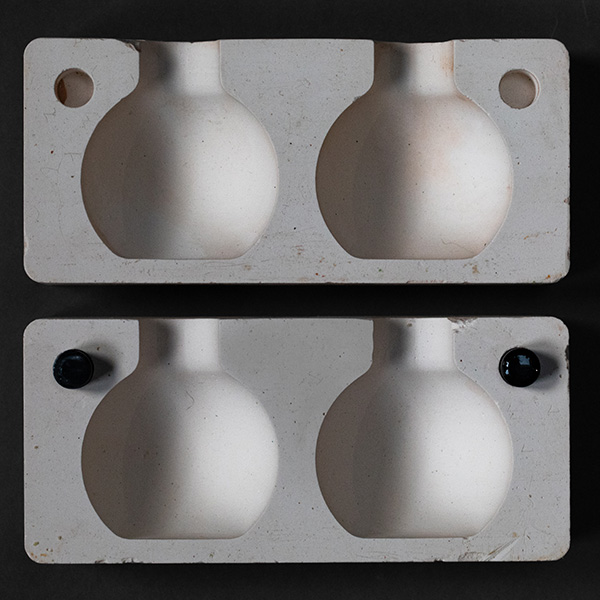
Preparing The Glazes
The aim is to formulate two glazes one with lower and the other with higher thermal expansion than the clay body being used. This is not easy! Prediction of glaze expansion coefficients is difficult and the situation with clay bodies is even more complex. The software known as ‘Insight’ which can be obtained from digitalfire.com is a good starting point and can be used to provide an initial estimate of thermal expansion coefficient from a glaze recipie. For the body, clay producers often give a thermal expasnion estimate and it can be used as a starting point. Varying the glaze can be done in several ways. In terms of the Seger unity formula, one of the easiest ways is to keep the bases constant and to vary the amount of silica, increasing it to reduce the thermal expansion. The alumina can be kept constant or maintined in constant ratio to the silica. This method generally allows a worthwhile (but modest) variation in expansion without a drastic change in the glaze appearance, durability and maturity. More dramatic changes in thermal expansion require alteration of the bases, a more complex process. Whatever the method, it is not always safe to assume that the coefficient will vary predictably, especially when altering the bases, the effect can be more complex than calculation predicts.
In the example here, the body I tested was one of my casting porcelains. It is a fairly conventional triaxial formulation using kaolin, ball clay, feldspar and silica with the flux level set to give near-zero porosity at cone 10. From experience of how glazes behave over it, I have a good idea of the expansion coefficient. The glaze is one of my food-safe black (very dark brown) glazes coloured using 8% of iron (III) oxide. Again, from experience, I have a good idea of the expansion coefficient. In this case, the two glazes differ only in the amount of silica, the low expansion has 4 moles on a unity bases, the high 3. One of the advantages of firing at cone 10 is that the glaze melts well and can tolerate even higher silica and still melt well. One thing that is very important here, and something I discovered early on in doing this type of test, is that iron oxide (in an oxidising firing) reduces the thermal expansion coefficient of the glaze. This one has 8% and it causes a substantial reduction in thermal expansion compared with the iron free version. Indeed, without the iron, both the low and high expansion versions of the glaze would craze over this body. The reason that iron does this is generally not well explained in the pottery literature. Because iron plays such an important role in the characteristics of magmas, it has been extensively studied by geologists and that body of literature is an excellent starting point for understanding the effect – there are some notes about it at the end of this article.
Glaze Blending and Application
I prepare the two glazes in the usual way for application by pouring by adjusting the specific gravity and then flocculating slightly with calcium chloride solution. In this case the target s.g. was 1.42 and enough flocculant to cause the glaze to gel approximately 3 seconds after stirring. I tested 5 levels of expansion in this series, 2 shock bottles for each glaze mixture to give a repeat for each. Because the two glazes have the same density, volumetric blending gives good results and a 10ml syringe is all that is needed. Glazing is then just a case of taking the bisc fired test bottles, pouring the glaze in, shaking for a few seconds and then draining. The only extra precaution I take in the glaze firing is to ensure that the bottles are protected from the kiln shelf by a good quality zircon based batt wash, this reduces the chance of the bottle being weakened by sticking to the shelf during firing.
The Test
The test I perform simulate a more extreme version of the thermal shock experienced when hot water is poured inside. I take the fired shock bottles and place them back in the kiln a an initial temperature of 150°C. They are thin walled and 15 minutes is enough time for them to reach the kiln temperature. I then pick up each of the bottles in turn with a pair of tonges and place them in a bucket of iced water making sure the outside gets fully submerged without initially letting any cold water get inside. In this way, the body of the bottle cools first and experiences temsion by shrinking onto the hotter glaze. Afterwards, I inspect the bottles for cracks. Some times cracking is dramatic, other times the cracks cannot be easily seen but can be inferred by the bottle counding dull when tapped. The bottles that don’t fail get put through the cycle again. A well-fitted glaze will survive an very large number of cycles (how many, I’ve not found out, it would take too long). Instead, after a few cycles of 150°C without failure, I raise the temperature by 20°C and continue. The best combinations I’ve found survive around 20 cycles of 250°C to iced water.
An Example
The images below show tests 9259-9263 together with the calculated thermal expansion coefficients in the absence of the Iron oxide. The porcelain body expansion coefficient I estimate to be around 6.5.
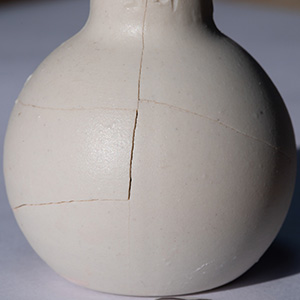
Test 9259. Calculated coefficient 6.86.
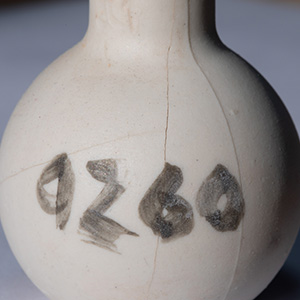
Test 9260. Calculated coefficient 7.04.
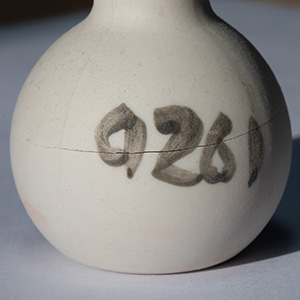
Test 9261. Calculated coefficient 7.22.
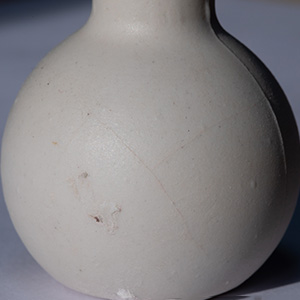
Test 9262. Calculated coefficient 7.40.
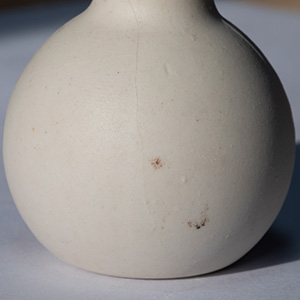
Test 9263. Calculated coefficient 7.58.
All survived 2 cycles at 150°C. The third cycle was at 170°C and 9259 failed. 9260 failed on the fifth cycle. The eighth cycle was at 180°C and 9261 failed. 9262 failed on the ninth and 9263 survived 13 cycles at 180°C before I stopped the test. I didn’t continue because looking at the failed pieces, I cuold see that the colour of the glaze was unsuitable and would be rejected on appearance anyway. However, the test clearly show the trend. An additional test that is useful is an unglazed piece as a reference.
The nature of the cracks are instructiuve. In 9259 the crack is quite wide, indicating that the body is being pushed outwards by the glaze, the cracks get narrower as the series progresses so that by 9262 the crack is hard to see but can be inferred by a dull sound.
Note also that the calculated expansion coefficients are clearly overestimates. It is because of the iron used as a colourant. In oxidation firings, iron oxide reduces thermal expansion quite significantly. Here, the evidence is that the reduction could be as much as from 7.58 predicted to 6.5. Additional evidence that this is so is that the clear, colourless glaze that I use with this porcelain has a calculated expansion of 6.86 and it doesn’t craze unless applied very thickly and subjected to repeated thermal shock.