Recently, I was asked if I could formulate a glaze based on a recipe known as ‘Old Forge B’. It is a type of glaze known as ‘Floating Blue’ so called because a blue opalescent layer of colour appears to float upon the glaze below. The mechanism is a high boron content that causes phase separation between silicate and borate glasses.
The original ‘Old Forge B’ sources boron from Gertsley Borate, an ingredient that can cause problems with glaze application and firing. This article is a good demonstration of how chemistry can be used to substitute for problem ingredients. It also is a good example of formulating a glaze suitable for brushing.
My other articles on glaze parameters, glaze additives and brushing glazes have the necessary background information.
This is not my glaze recipe. The credit goes to ‘old forge creations’ and this excellent article on systematic glaze testsing.
Example of a Floating Blue
I tested a floating blue glaze in 2022 in one of my cone 9 crystalline firings. The recipe was similar to the one used in this article.
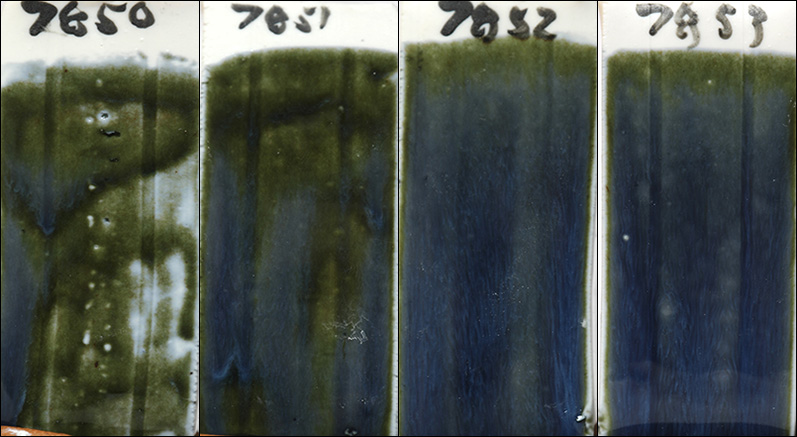
These are extruded Royale porcelain test forms, each face is approximately 130mm x 40mm. Thickness varies across the series, G400, G600, G800 and G1000. Thickness is important in developing the floating blue effect.
Reformulating Old Forge B
The calculations needed to substitute glaze materials are straightforward but tedious to perform manually. There are many commercially available programs that automate the process, ‘Insight’ available from Digitalfire for example. I use my own program, written specifically for the unusual requirements of crystalline glazing.
This is the recipe for Old Forge B together with my calculated oxide analysis. Numbers after the ingredient names are weights in grams, numbers after the oxide names are moles normalised to flux unity.
Nepheline syenite* 35 Na2O 0.21 Al2O3 0.51 SiO2 3.33
Gertsley borate 23.5 K2O 0.14 B2O3 0.35
Silica 23.0 CaO 0.49
China clay 11.0 SrO 0.08
Calcium carbonate 4.5
Strontium carbonate 3.0
+Rutile 4
+Bentonite 2
+Manganese dioxide 2
+Cobalt carbonate 1
*using the analysis for North Cape Nepheline.
The materials I will substitute are the Gertsley borate and nepheline syenite. Many frits are available to source the boron, here I use Ferro 3195. Nepheline syenite is not a problem, it does have a reputation for causing problem for glaze liquids because of slight solubility, but I have not found this to be an issue. Here, I substitute it for convenience because I use a lot of feldspar in my work. I have chosen Euroarce FC-200 feldspar, widely available in the UK and marketed as ‘potash feldspar’. I also introduce talc as a source of magnesium as the gertsley borate contains it but not the replacement frit. For the clay, EPK is a good choice but grolleg would also be suitable. I don’t attempt to maintain the same individual amounts of sodium and potassium oxides, instead, I treat them as equivalent.
#1
Potash Feldspar 38.6 NaKO 0.35 Al2O3 0.51 SiO2 3.33
Ferro 3195 frit 30.4 MgO 0.08 B2O3 0.35
Silica 8.8 CaO 0.49
China Clay 8.4 SrO 0.08
Calcium Carbonate 7.6
Strontium Carbonate 3.3
Talc 2.8
One problem with this is the clay content is rather too low for give good glaze application characteristics. This can be solved by sourcing the main alkali oxides from a frit instead of feldspar giving recipe #2.
#2
Ferro 3110 frit 26.6 NaKO 0.35 Al2O3 0.51 SiO2 3.33
Ferro 3195 frit 26.8 MgO 0.08 B2O3 0.35
Silica 10.1 CaO 0.49
China Clay 25.3 SrO 0.08
Calcium Carbonate 5.1
Strontium Carbonate 3.2
Talc 2.8
Now the clay content is rather too high, at 25% there is a risk of the glaze cracking as it dries. Recipes #1 and #2 can be combined to give the ideal clay content of 20%.
#3
Ferro 3110 frit 18.2 NaKO 0.35 Al2O3 0.51 SiO2 3.33
Ferro 3195 frit 27.9 MgO 0.08 B2O3 0.35
Silica 9.7 CaO 0.49
China Clay 20.0 SrO 0.08
Calcium Carbonate 5.9
Strontium Carbonate 3.2
Talc 2.8
Potash Feldspar 12.2
+Rutile 4
+Manganese Dioxide 2
+Cobalt Carbonate 1
#3 has the correct amount of clay to create a glaze that applies well by either brushing or dipping. The 2% bentonite is no longer needed, the clay will take care of the suspension.
A Brushing Version
Here is my first attempt at formulating a brushing vesion. It uses 1.5% each of CMC and Vee gum, both introduced as premixed semi-liquids, and has an overall solid loading of F0.45. I made a mistake and used cobalt oxide instead of the intended cobalt carbonate which means that the amount of cobalt going into the glaze is more than in the Old Forge B recipe. I mixed it by ball milling, first adding all the ingredienmts except the CMCSOL, milling for 30minutes (stage 1) and the adding the CMCSOL and milling for a further 30 minutes (stage 2). After stage 1 the glaze was extremely fluid, with viscosity similar to that of water. After stage 2 it was transformed into a very viscous semi-solid.
Ferro 3110 frit 18.2 NaKO 0.35 Al2O3 0.51 SiO2 3.33
Ferro 3195 frit 27.9 MgO 0.08 B2O3 0.35
Silica HIM2 9.7 CaO 0.49
Grolleg china clay 20.0 SrO 0.08
Calcium carbonate 5.9
Strontium carbonate 3.2
Talc 2.8
FC-200 feldspar 12.2
+Rutile 4
+Manganese dioxide 2
+Cobalt oxide 1
Dispex 0.2
CMCSOL40 44
VGT80 22
Water 70
F0.45
I tested the glaze on a Royale porcelain (Valentine clays) extrusion at thicknesses of G600, G800 and G1200. In addition, anticipating that glaze would run at the thicker applications, I used my magnesium satin white, applied at G600 as a catch glaze on the bottom 20mm of the test surface with the glazes brushed together with no overlap. An additional test to see how the glazes would react when layered was a 40mm length of magnesium glaze with 20mm of overlap and the floating blue applied at G800.
Brushing characteristics for G600 are very good. The glaze is semi-solid and loads on the brush well without risk of dripping. Drying is sufficiently slow to allow an even coat at G600 to be built up without waiting for intermediate coats to dry. At G800 it takes longer and some time must elapse to allow the initial layer to dry a little before continuing. At G1200 is is necessary to wait twice for intermediate layers to dry, the whole process requiring about 10 minutes. I’d say that this formulation would be fine provided that the application thickness is not required to go over G800. For G1200, I would adjust the quantities to give slightly fater drying, something like 1% CMC rather than 1.5% and maybe a slight increase in solid loading to F0.47. Of course, all of this depends on the absorbancy of the bisc ware and on the surface area required to be covered. If the surface area were large, the additional time for application allowed by 1.5% CMC might be needed even at G1200.
Fired Results
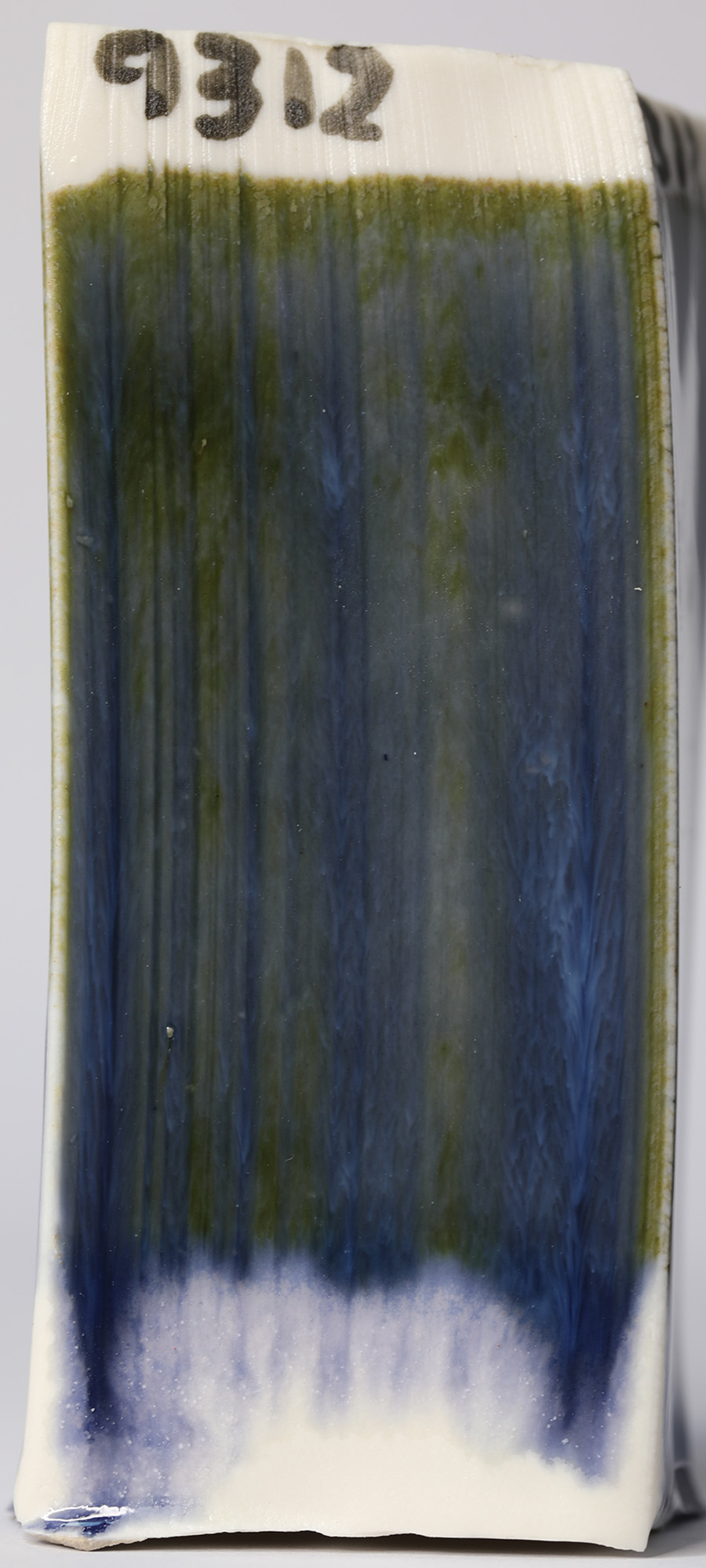
G600
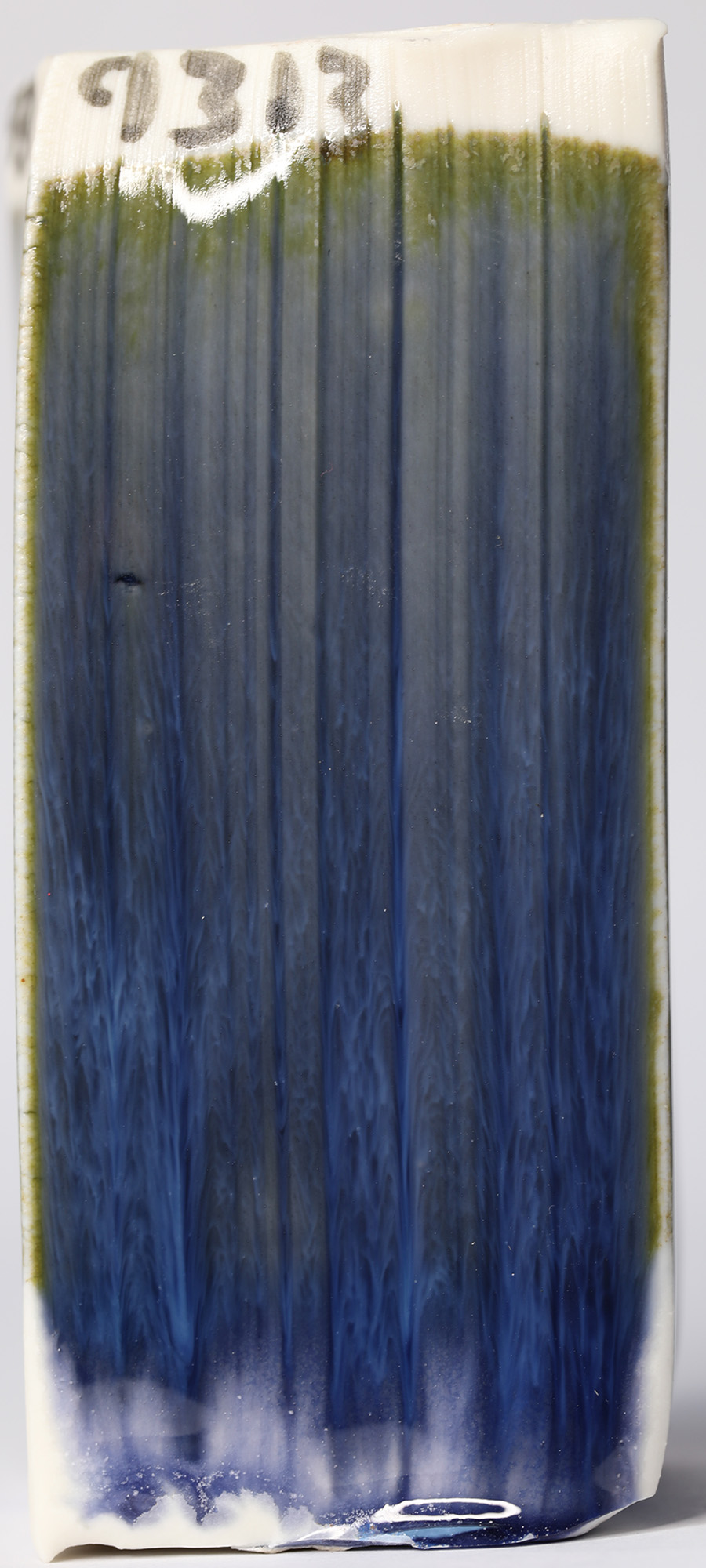
G800
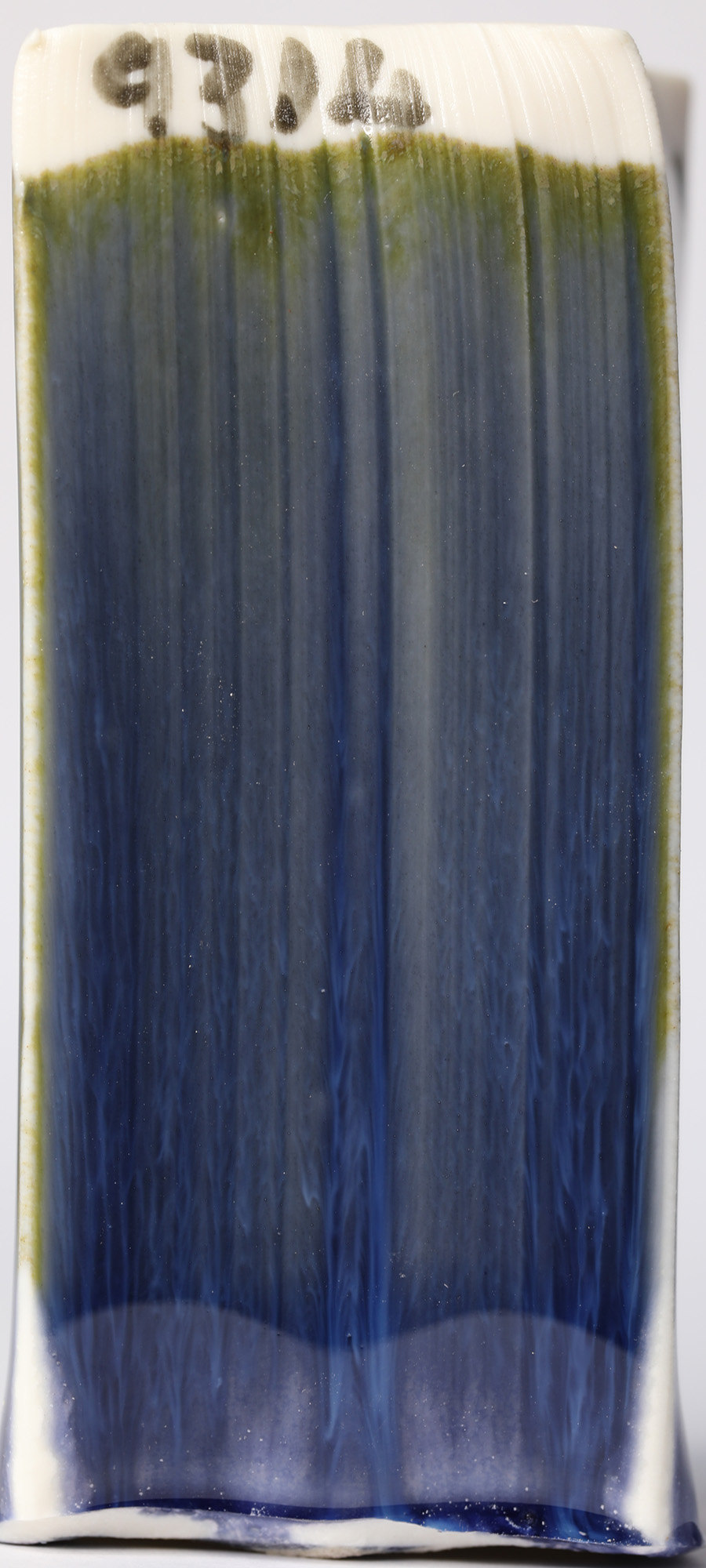
G1200
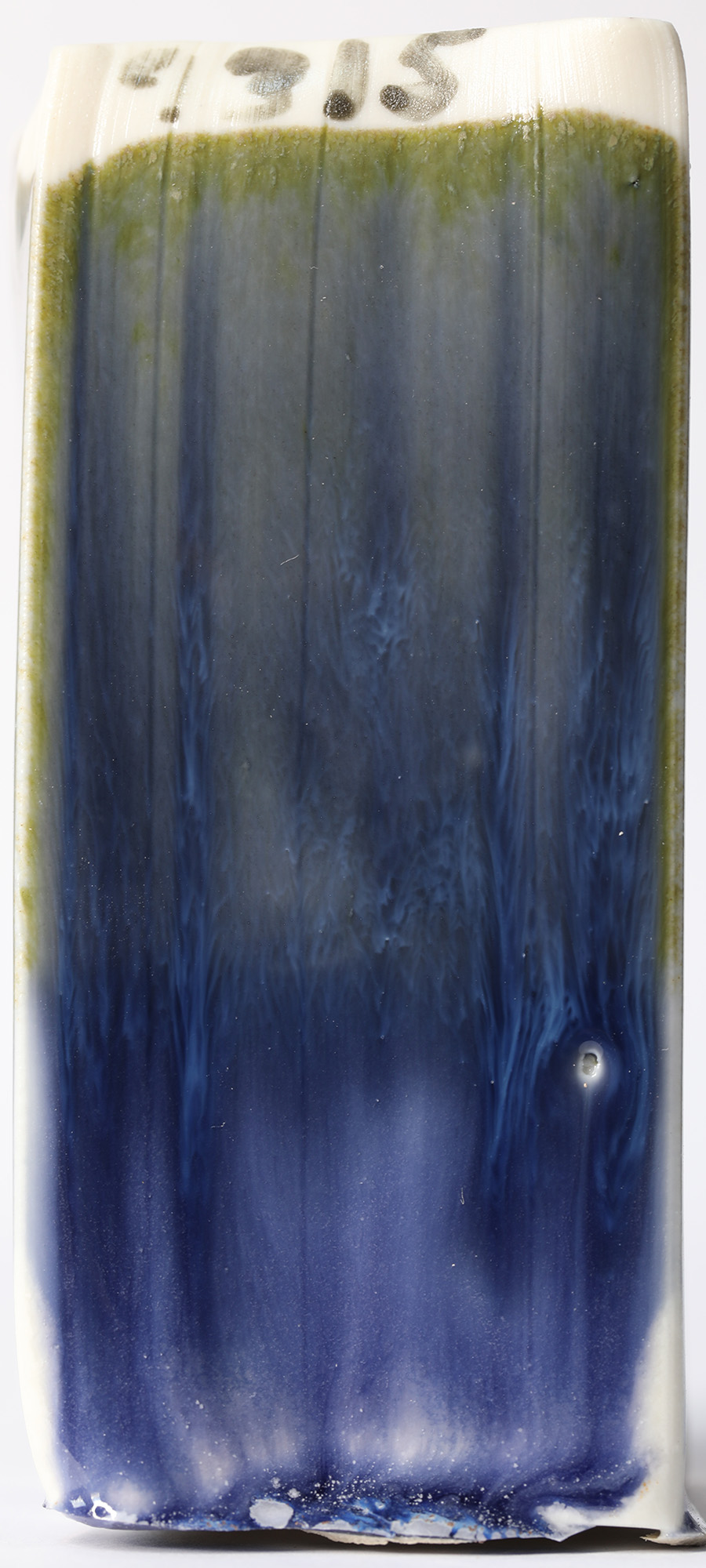
G1200, 20mm overlap
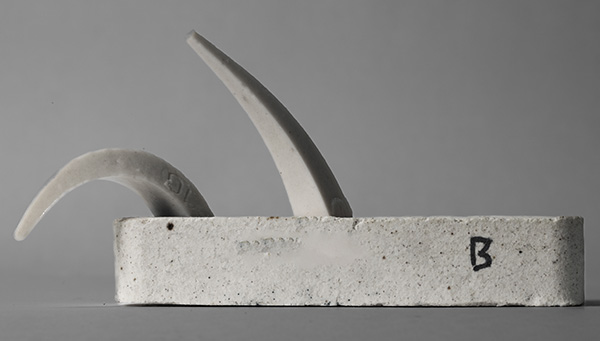
Orton cones 10 and 11
The witness cones were next to the test piece. Cone 10 is down, cone 11 starting to bend. All the glazes have run somewhat, at G600 the catch glaze can still be seen and the interaction is attractive. The floating blue is not well developed at G600. By G800 the effect is good and there appears to be no need to go as thick as G1200. Where the glazes overlap at G800 the magnesium glaze underneath does modify the appearance of the floating blue but the effect is attractive and could be used for creative effect. Old Forge B is a cone 6 recipe, it is remarkable that it has performed reasonably well at cone 10 without modification to the flux content. It is very likely that this version would perform better at a lower temperature, maybe as low as cone 6.
One additional feature of the G600 test is the hint of a pink colour where the floating blue has interacted with the magnesium glaze. This is a characteristic colour associated with cobalt in glazes containing a lot of magnesium and is often exploited to give lavender colours. It is a mechanism that also works in zinc silicate crystalline glazes. I produced a lot of work in 2007 for my exhibition in Gmunden, Austria, using it.